Understanding the Differences Between 2-Plate and 3-Plate Molds in Injection Molding
Injection molding is a versatile manufacturing process that enables the precision and efficiency of the production of complex plastic parts. A key decision in this process is selecting the right mold type. The two primary designs—2-plate and 3-plate molds—each offer unique features, advantages, and applications. By understanding their differences and the specific scenarios they suit, manufacturers can make informed choices to optimize production outcomes.
What is a 2-Plate Mold?
A 2-plate mold, also known as a two-plate mold, is the most straightforward and most commonly used injection mold design. It consists of two main sections:
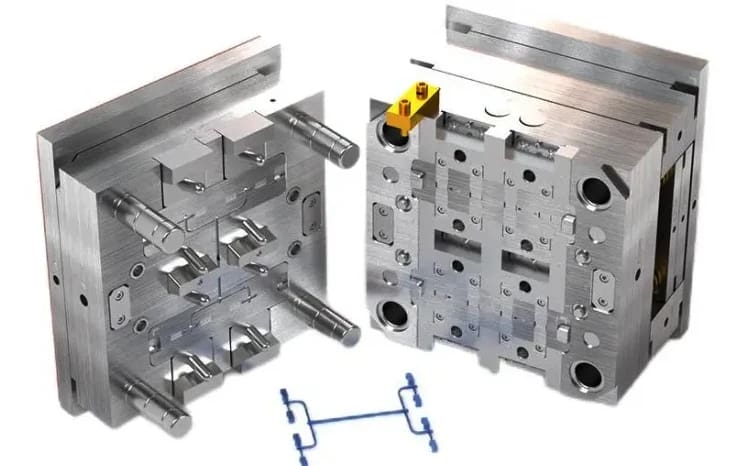
1. Cavity Plate: It contains the final part’s cavity or impression, defining its outer shape and surface finish.
2. Core Plate: Complements the cavity plate and shapes the inner surface of the part. It often includes ejector pins for part removal.
When the mold opens, it separates along a single parting line, ejecting the molded part. The runner system channels molten plastic from the injection nozzle to the cavities, remains attached to the molded part, and must be removed manually or mechanically.
Key Features of a Two-Plate Mold:
• Single Parting Line: Simplifies the mold design and operation.
• Integrated Runner System: Runners are on the same plane as the molded part.
Advantages of 2-Plate Molds:
• Simplicity: The straightforward design reduces tooling costs and maintenance needs.
• Cost-Effectiveness: Ideal for budget-conscious projects, particularly with high production volumes.
• Fast Cycle Times: Simpler mechanics enable quicker mold opening and closing.
• Durability: Robust construction handles the stress of molding large or straightforward parts.
Limitations of Two-Plate Molds:
• Manual Runner Removal: Requires additional steps to separate parts from runners.
• Limited Design Flexibility: Less suitable for intricate parts requiring multiple gates.
Example Applications:
2-plate moulds are ideal for larger, straightforward parts such as automotive panels, flat plastic containers, or industrial equipment components.
Two-Plate Mold Design
The two-plate mold is one of the simplest and most widely used injection mold designs, offering numerous advantages for manufacturing plastic components. This mold design comprises two primary sections: Side A (the fixed side) and Side B (the movable side). During the injection moulding process, Side A remains stationary, while Side B moves to facilitate the ejection of moulded parts.
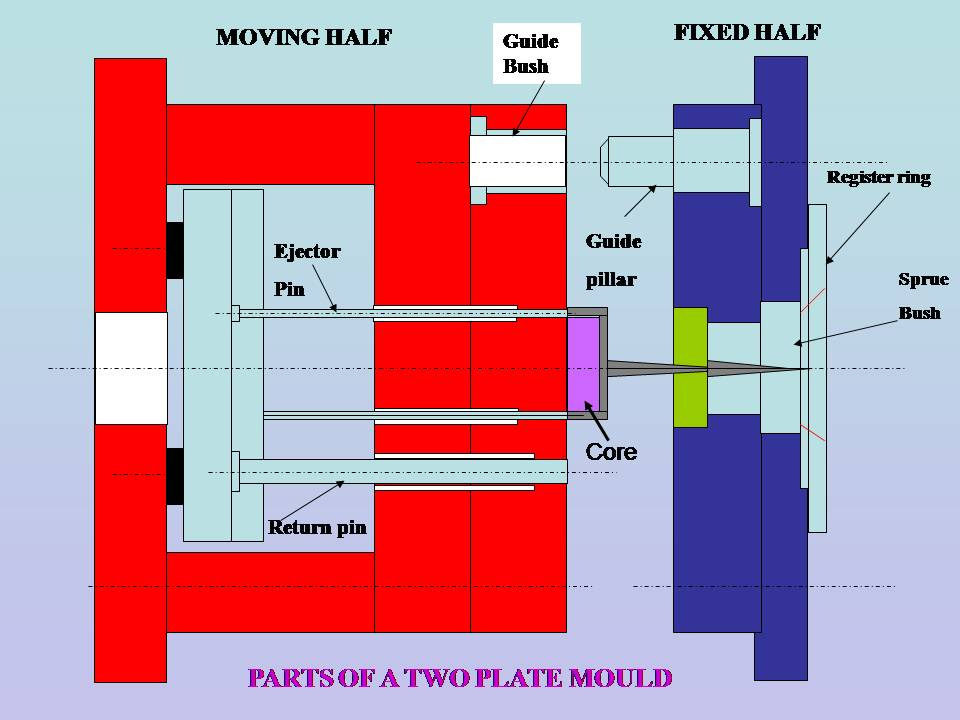
Below are the key components of a two-plate mold and their functions:
-
- Return Pin
- Ensures the ejector pin retracts before the mold closes, preventing damage to moulded products.
- Sprue
- Channels the molten material from the injection nozzle into the mold cavity, facilitating uniform flow.
- Ejector Guide Pin
- Provides precise guidance for the ejector system to ensure accurate ejection of moulded parts.
- Guide Pin and Guide Bushing
- Work together to maintain alignment and precision between Side A and Side B during mold operation.
- Location Ring
- Aligns the injection nozzle with the sprue, ensuring the proper flow of molten material into the mold. It is typically manufactured from durable materials like S55C to withstand wear and tear.
This straightforward yet practical design is widely favoured for its simplicity, reliability, and cost-efficiency in producing high-quality plastic components.
What is a 3-Plate Mold?
A 3-plate mold features an additional plate, called the runner plate, making it more complex and versatile than a 2-plate mold. It consists of three main sections:
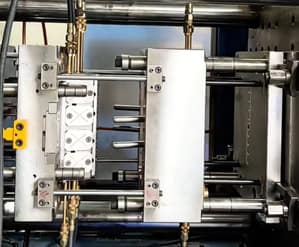
1. Cavity Plate: Contains the cavity for the part’s outer shape.
2. Runner Plate: Houses a separate channel system for the flow of molten plastic, allowing multiple gating points.
3. Core Plate: Complements the cavity plate and includes ejector mechanisms for part removal.
This mold separates into three planes during operation: one for the molded part, one for the runner system, and one for the gating system. This ensures that runners and gates are automatically detached from the part during ejection.
Key Features of a Three-Plate Mold:
• Two Parting Lines: Ensures clean separation between the part and runner system.
• Flexible Gate Placement: Allows gates to be positioned anywhere on the part, supporting intricate designs.
Advantages of 3-Plate Molds:
• Versatility: Accommodates complex geometries, undercuts, and multi-gated parts.
• Reduced Cosmetic Defects: Strategically placed gates minimize weld lines and sink marks.
• Automatic Runner Separation: Enhances production efficiency and reduces post-molding labor.
Limitations of Three-Plate Molds:
• Higher Costs: Complexity results in a higher upfront tooling investment.
• Longer Cycle Times: Additional steps for separation extend production cycles.
Example Applications:
3-plate molds are preferred for small, detailed parts like electrical connectors, medical devices, and high-precision automotive components.
Critical Differences Between 2-Plate and 3-Plate Molds
Feature | 2-Plate Mold | 3-Plate Mold |
Construction | Simpler, two sections | More complex, with three sections |
Parting Lines | Single parting line | Two parting lines |
Runner Separation | Manual or requires effort | Automatic during mold opening |
Gate Placement | Limited | Flexible for optimal design |
Applications | Large or simple parts | Small or intricate parts |
Cost | Lower initial cost | Higher initial cost |
Cycle Time | Faster | Slightly longer due to the added steps |
Choosing Between 2-Plate and 3-Plate Molds
The choice between these mold types depends on several factors:
- Part Complexity: For simple designs like flat panels or crates, a 2-plate mold is sufficient. For intricate parts requiring precision or aesthetic quality, a 3-plate mold is ideal.
- Production Volume: In high-volume manufacturing, the automatic runner separation of a 3-plate mold offsets its higher cost by improving efficiency.
- Budget Constraints: For cost-sensitive projects, the simplicity of a 2-plate mold makes it the preferred option.
Conclusion
The decision to use a 2-plate or 3-plate mold depends on the specific requirements of your injection molding project.
While 2-plate moulds are cost-effective and durable for simple parts, 3-plate moulds provide precision and flexibility for complex designs.
At DSW, we specialize in designing and manufacturing 2-plate and 3-plate moulds to meet various needs.
Whether you’re producing large industrial parts or intricate high-precision components, our expertise ensures that your molds deliver exceptional results.
Contact us today to discuss the best solution for your next injection molding project!