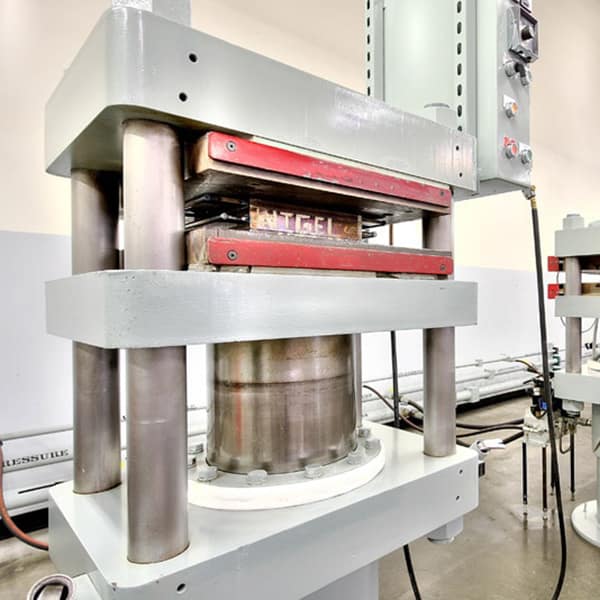
What Is Compression Molding?
Composite Compression moulding is a manufacturing process that involves shaping composite materials under heat and pressure to create strong, lightweight, and complex parts. In this method, a composite material—typically made of a combination of a polymer matrix (like thermosetting resins such as polyester, epoxy, or vinyl ester) and reinforcing fibres (such as glass, carbon, or aramid fibres)—is placed into a heated mold cavity.. This process, called plastic compression moulding, involves placing a raw material into an open mold cavity. The mold is then closed by applying pressure using a press, allowing the material to flow, fill the cavity, and conform to the desired shape. Heat and pressure are maintained until the material cures or solidifies, after which the finished product is removed. Compression moulding can manufacture a variety of parts and components with precise dimensions and complex geometries, including automotive parts like bumpers, engine covers, and interior trim; electrical components such as insulators, circuit breaker casings, and switch housings; and consumer items like kitchenware, appliance parts, and sports equipment.
Compression Mold
Compression moulds are used in various manufacturing processes, including Bulk Molding Compound (BMC), Sheet Molding Compound (SMC), and other composite materials.
Thermoset Compression Molding is a manufacturing process specifically designed to shape thermosetting plastics into finished parts. Compression forming is widely utilised for creating parts with precise dimensions and complex geometries, making it highly applicable in the automotive, electrical, and consumer goods sectors.
Advantages of Composite Compression Molding
1. High Strength-to-weight Ratios: In compression molding, composite materials are often reinforced with continuous or chopped glass fibers, carbon fibers, or aramid fibers. These fibers have excellent tensile strength and stiffness, and the polymer matrix distributes the load evenly throughout the part.
Material Tailoring: The fiber-to-resin ratio can be altered to optimize mechanical qualities for specific applications. For example, increasing fiber content can improve tensile strength and stiffness, making parts ideal for structural applications in the aerospace and automotive industries.
Weight reduction: By replacing metal parts with lightweight composite components, manufacturers can obtain significant weight savings—up to 30-60% lighter than steel—which is critical in applications like as fuel-efficient vehicles and airplanes.
2. Precision and Dimensional Stability: Composite compression molding uses matched die tooling, which perfectly aligns the top and lower portions of the mold. This ensures that even intricately detailed items have consistent dimensions and surface finishes.
The curing process of thermoset composites reduces shrinkage and warping, resulting in great dimensional precision and tight tolerance control (typically within ±0.005 inches). This precision is critical for fit-and-function applications in electrical housings and automobile components.
Thermal Stability: Composite materials are exceptionally thermally stable, retaining their structure and mechanical qualities across a wide temperature range, making them perfect for under-the-hood car components and high-temperature industrial parts.
3. Cost-effective for large-scale production:
Composite moulding has short cycle times, ranging from 2 to 5 minutes, depending on part thickness and material type, making it ideal for high-volume production runs. This is far faster than other composite manufacturing technologies’ hand lay-up or autoclave processes.
Mold Reusability: Compression molds, often composed of hardened tool steel or aluminum, are long-lasting and can sustain hundreds of molding cycles without substantial wear, resulting in a lower per-part production cost.
Low Material Waste: The procedure reduces material waste because the raw material is pre-measured and placed directly into the mold instead of injection molding, which may require surplus material for runners and sprues.
4. Flexibility in Design:
intricate Geometries: Compression molding can produce pieces with deep draws, thin walls, ribbing, and intricate curves that other molding processes cannot. This adaptability is perfect for components like car panels and aircraft fairings, which require weight reduction and aerodynamics.
Variable Wall Thicknesses: The approach enables the design of sections with different wall thicknesses inside a single part, improving structural integrity where necessary while reducing weight elsewhere.
Surface Finish: Composite compression molding can create smooth or textured surfaces, eliminating the need for extra finishing procedures like sanding or painting. This functionality is handy for consumer products where aesthetic appeal is crucial.
Insert Integration: Metal inserts or threaded components can be incorporated directly into the part during molding, eliminating the requirement for post-molding assembly and increasing the end product’s load-bearing capability.
Types of Composites
Sheet molding compound (SMC) is manufactured separately from the pressing operation. Through a highly automated process, chopped fibre and thermoset resin matrices are blended to create a semi-flexible sheet, which is subsequently moulded into a part.
Bulk Molding Compound (BMC) is a blend of thermosetting resin, such as polyester or vinyl ester, reinforcement fibres, fillers, and additives. This mixture is usually supplied in bulk, commonly as pellets or sheets. Manufacturers frequently employ BMC in compression moulding processes to manufacture durable, corrosion-resistant, and dimensionally precise parts for automotive, electrical, and appliance manufacturing industries.
The Features of Compression Mold
These molds have several features that make them suitable for such applications:
Two-Piece Design: Compression molds typically consist of two halves, the cavity and the core. This design allows easy material loading and removal of the finished part after moulding.
Precision Machining: By precisely machining the compression moulds, you can ensure that your final product meets all your specifications. It includes precise dimensions, high-quality surfaces, and intricate detail.
Heat Resistance: Compression moulds are often constructed of materials that can withstand high temperatures, as the moulding process involves heating the material to facilitate curing. Common mold materials include hardened steel, aluminium, and various alloys.
Venting System: Venting in compression moulds prevents air or gas pockets from forming within the moulded part. This allows the release of trapped air during the moulding procedure, resulting in a more uniform and defect-free part.
Cooling Channels: Compression moulds often incorporate passages or channels to circulate fluids such as water or oil. These channels help to dissipate mould heat and increase productivity by reducing cycle time.
Ejector System: The object must be removed from the mold after the moulding process. In compression moulds, an ejector system, such as sleeves or pins, is usually included to help release the moulded object from the cavity.
Durability: Composite moulds are designed to withstand repeated use over many moulding cycles. Therefore, they must be constructed from durable materials and withstand maintenance and repairs.
High-Volume Production and Precision Tolerance
Composite compression molding is highly efficient, especially for high-volume manufacturing. SMC compression molding and BMC compression molding are ideal for producing large quantities due to their short cycle times, ranging from 2 to 4 minutes. Durable, precision-machined tool steel moulds allow annual production volumes exceeding 500,000 units, ensuring cost-effectiveness and scalability for industries requiring mass production.
Thermoset compression molding is well-known for its precision tolerance. SMC formulations, for instance, exhibit excellent dimensional stability, and matched-die tooling ensures that parts meet tight tolerance requirements and supports high-precision assemblies.
Applications of Compression Molding
Compression molding is commonly used in the automotive, aerospace, electrical, and consumer goods industries for producing components such as:
Automotive: Body panels, bumpers, engine covers, and interior trim.
Electrical: Insulators, circuit breaker components, and housings.
Consumer Goods: Kitchenware, appliance parts, and sports equipment.
Conclusion
Compression molding remains an efficient, cost-effective manufacturing method for producing complex, high-strength components. Whether through SMC compression molding, BMC compression molding, or thermoset compression molding, this process offers significant advantages in dimensional stability, precision, and high-volume production, making it a preferred choice in automotive, electrical, and consumer goods manufacturing.
No comment