Understanding Mold Materials in Plastic Injection Molding
In the realm of plastic injection molding, selecting the appropriate mold material is crucial for achieving high-quality and cost-effective production. Mold materials play a pivotal role in determining the durability, thermal conductivity, and overall performance of the mold. This article aims to provide insights into the different types of mold materials commonly used in plastic injection molding processes.
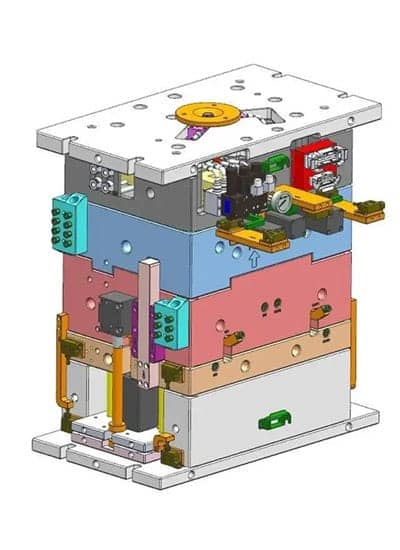
Mold Material Selection
The choice of mold material significantly impacts the success of injection molding operations. Factors such as part complexity, production volume, material compatibility, and cost considerations influence the selection process. Optimal mold materials ensure dimensional accuracy, minimize part defects, and enhance overall productivity.
Mold Material Options
a. Steel Alloys:
Tool Steel: Known for its excellent wear resistance, high hardness, and toughness, tool steel is widely used for molds subjected to high-pressure and high-volume production.
Stainless Steel: Preferred for applications requiring corrosion resistance, stainless steel molds are suitable for molding materials with corrosive properties.
Prehardened Steel: With good machinability and moderate hardness, prehardened steel offers a balance between cost and performance for many injection molding applications.
Considerations for Mold Material Selection:
a. Part Complexity: Complex parts with intricate details may require higher hardness and wear resistance in the mold material to ensure dimensional accuracy and prolong the mold’s lifespan.
b. Material Compatibility: Different plastic resins have varying processing temperatures, chemical properties, and flow characteristics. Mold materials must be chosen to withstand the specific requirements of the intended plastic material.
c. Production Volume: The expected production volume influences the choice between steel and aluminum molds. High-volume production typically justifies the use of more durable and long-lasting steel molds, while aluminum molds are suitable for lower-volume runs.
d. Cost Considerations: Budgetary constraints may dictate the selection of mold materials. Steel molds generally involve higher initial costs but offer better long-term durability, whereas aluminum molds are more cost-effective for shorter production runs.
The selection of mold material should be based on a thorough evaluation of the specific requirements of the molding application, including part complexity, production volume, resin compatibility, cooling requirements, and cost considerations. Working with experienced mold designers or mold manufacturers can provide valuable insights and expertise in selecting the most appropriate mold material for your specific needs.
No comment