Polycarbonate (PC) Plastic: From Transparency to Impact Resistance
Polycarbonate (PC) is a versatile and durable thermoplastic polymer celebrated for its exceptional impact resistance and natural transparency. Widely utilized across various industries, PC offers robust mechanical properties that cater to diverse needs through specialized manufacturing services:
- injection molding: Produces bright green components with cylindrical and forked features.
- CNC Machining: Crafts black round parts with twin clasp-like extensions.
- 3D Printing: Creates light grey pieces with intricate internal structures.
Polycarbonates Injection Molding
Injection molding is the predominant method for producing polycarbonates and their blends. Due to its high viscosity, polycarbonate is typically processed at elevated temperatures to lower its viscosity. The molten polymer is injected into a mold under high pressure. As the mold cools, it imparts the desired shape and properties to the polymer. This technique is commonly used for manufacturing polycarbonate bottles and plates. Given polycarbonate’s poor flow characteristics, it is essential to avoid skinny wall sections.
Typical Settings for Injection Molding Various Polycarbonate Resins
Resin Type | Melt Temperature (°C) | Mold Temperature (°C) | Molding Shrinkage (%) |
---|---|---|---|
Polycarbonate (PC) | 280-320 | 80-100 | 0.5-0.8 |
High Heat Polycarbonate | 310-340 | 100-150 | 0.8-0.9 |
Filled Polycarbonate | 310-330 | 80-130 | 0.3-0.5 |
PC/ABS | 240-280 | 70-100 | 0.5-0.7 |
PC/PBT | 250-270 | 60-80 | 0.8-1.0 |
PC/PET | 260-280 | 60-80 | 0.6-0.8 |
The Versatility of Polycarbonate in CNC Machining
PC is increasingly favoured in CNC machining due to its exceptional impact resistance and transparency. Its ease of machining allows for various operations, such as milling and drilling, while maintaining precise tolerances essential for high-accuracy applications.
However, PC plastic is heat-sensitive, so managing cutting speeds and using coolants is crucial to prevent softening. Due to its strength and aesthetic appeal, this thermoplastic is ideal for safety equipment, electronic housings, and optical devices.
Polycarbonate’s durability, lightweight nature, and machining versatility make it a top choice in modern manufacturing, suitable for small-scale projects and large production runs.
Advantages of Polycarbonate
1. Transparency: PCs excel at light transmission, which is crucial for applications like eyeglass lenses and transparent protective shields.
2. Impact Resistance: PC is renowned for being virtually unbreakable, making it ideal for safety goggles, bulletproof glass, and automotive headlight lenses.
3. Heat Resistance: PCs can withstand high temperatures without deformation and are used in microwave-safe cookware and LED light covers.
4. Lightweight: Polycarbonate is significantly lighter than glass, making it easier to handle and install in various applications. Despite its strength, PC is relatively light, benefiting industries such as aerospace and automotive for weight reduction.
5. UV Resistance: PC’s ability to resist ultraviolet radiation makes it suitable for greenhouse panels and outdoor protective covers.
6. Electrical Insulation: PCs are excellent insulators of electrical and electronic components, preventing short circuits and electrical hazards.
7. Ease of Processing: Polycarbonate can be quickly processed using methods such as injection moulding, extrusion, and thermoforming, allowing for a wide range of applications.
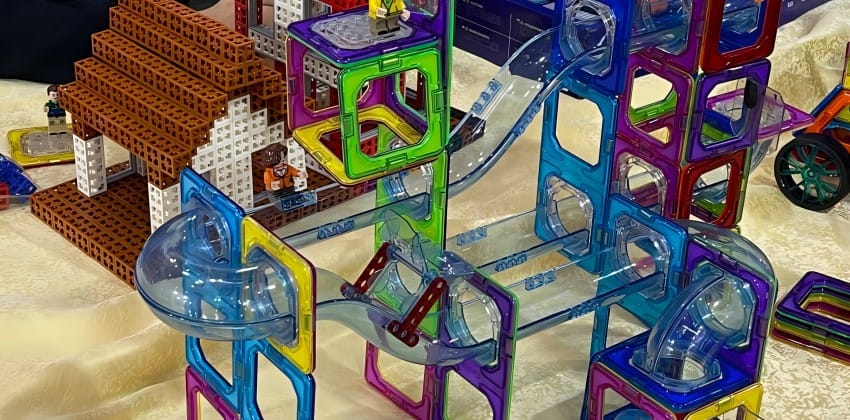
Disadvantages of Polycarbonate
- Flammability: While not inherently flame retardant, additives can be applied to meet specific fire safety standards.
- Chemical Sensitivity: PC may react with certain chemicals and cleaning agents, requiring careful selection of materials.
- Cost: PC can be more expensive than other plastics due to its specialized properties.
- Food Contact Suitability: Some types of PC may not be suitable for direct food contact, though BPA-free options exist.
Applications of Polycarbonate
PC’s exceptional impact strength and transparency make it indispensable across numerous industries:
-
- Safety Equipment: Used in safety goggles, face shields, and helmets.
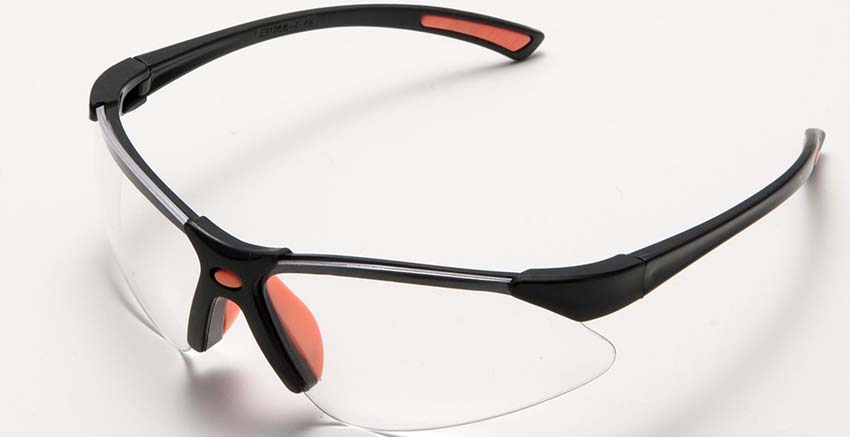
- Optical Lenses: These are employed in eyeglass and camera lenses for optical clarity.
- Automotive: Applications include headlight lenses, interior components, and sunroofs.
- Medical Devices: Used in incubators, surgical instruments, and dialysis machines.
- Consumer Products: Widely used in water bottles and food containers.
- Aerospace: Utilized in aircraft windows and interior components.
- Lighting: PC is found in fixtures, fluorescent tube covers, and LED light diffusers.
- Electronics: Used in laptop casings, smartphone covers, and electronic device components.
- Sporting Goods: Applications include helmets, protective gear, and sports goggles.
- Signage and Displays: Used for outdoor signs, display screens, and advertising materials.
Comparisons with Similar Materials
Acrylic (PMMA): PMMA offers transparency and optical clarity like PC but lacks PC’s impact resistance, making it suitable for applications such as signage and display cases.
PETG (Polyethylene Terephthalate Glycol-Modified): Known for transparency and impact resistance, PETG is a safer alternative to PC in applications sensitive to BPA concerns.
Polyethylene (HDPE or LDPE): Lightweight and impact-resistant, commonly used where chemical resistance and flexibility are prioritized, such as in bottles and liners.
Future Trends and Innovations
Looking ahead, advancements in PC technology are focusing on:
- Environmental Impact: Research into PC’s recyclability and sustainability efforts.
- Advanced Applications: Emerging uses in renewable energy sectors and wearable technology.
- Innovative Manufacturing: Development of PC composites and novel production techniques.
Conclusion
Polycarbonate remains at the forefront of modern materials, offering unmatched versatility and durability across industries. As innovations evolve, the PC’s role in shaping safer, more efficient, sustainable products remains pivotal. Whether in enhancing safety, improving optical clarity, or driving technological advancements, PC continues to redefine possibilities in manufacturing and design.