Understanding the Density of Nylon Plastic
Nylon, a versatile synthetic polymer, is widely used in manufacturing, especially in plastic injection moulding. Known for its strength, flexibility, and resistance to wear, nylon is used in applications from automotive components to electronics and consumer goods. Density is a critical property that influences nylon’s performance and suitability for specific applications.
Nylon is a synthetic polymer characterized by a molecular structure that consists of repeating amide groups (–CONH–). This structure forms through polymerization, where monomers like hexamethylene diamine and adipic acid chemically bond to create long chains. The resulting polymer’s molecular configuration enhances its strength, flexibility, and resistance to wear. Nylon’s crystalline nature and the hydrogen bonds between its chains contribute to its durability and mechanical properties. These features make nylon suitable for various applications, including textiles, automotive parts, and industrial components. Its robust structure is vital to its versatility and performance across industries. This article explores the density of nylon, how it varies across different types, and why it matters in industrial applications.
What is Density?
Density measures mass per unit volume, often expressed in grams per cubic centimetre (g/cm³) or kilograms per cubic meter (kg/m³). In practical terms, density determines how “heavy” or “light” a material feels for a given volume. For materials like nylon, density provides insights into mechanical properties such as strength, stiffness, and thermal stability. However, it is moisture-absorbent, which can impact its properties.
Understanding a material’s density is essential in injection moulding because it affects how it flows, solidifies, and performs under different conditions. High-density nylons are generally more rigid and stable, while low-density nylons may offer more flexibility and reduced weight.
Types of Nylon and Nylon Density Comparison
Nylon is available in several types, each with unique density characteristics that suit various industrial needs. Here’s an overview of some common types of nylon and their density comparison:
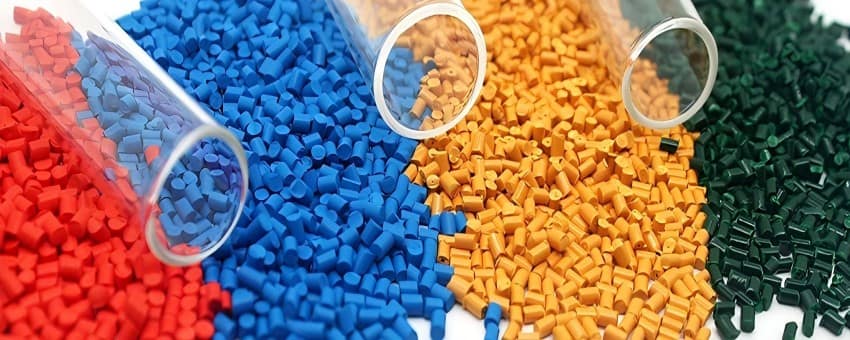
- Nylon 6: This type has a density of approximately 1.13 g/cm³. Known for its toughness and impact resistance, Nylon 6 is used in applications that require flexibility, such as gears, bearings, and textiles.
- Nylon 6/6: With a slightly higher density of 1.14 g/cm³, Nylon 6/6 offers greater strength and heat resistance than Nylon 6. It’s often chosen for applications that experience high stress and temperature, such as automotive engine parts and electrical connectors.
- Nylon 6/12: This variant has a density of about 1.05–1.10 g/cm³, lower than Nylon 6 and 6/6. It absorbs less moisture, making it ideal for applications that require dimensional stability in humid conditions, such as air conditioning components.
- Glass-Filled Nylon: By incorporating glass fibres, glass-filled nylon achieves a 1.35 to 1.50 g/cm³ density. This reinforced type is stiffer, stronger, and less flexible, making it suitable for structural components like brackets, pump housings, and valve bodies.
- Mineral-Filled Nylon: With a density between 1.20 and 1.40 g/cm³, mineral-filled nylon offers improved dimensional stability and rigidity. It’s used for precision parts, such as gears and threaded fasteners, where accuracy is crucial.
- Carbon-Filled Nylon: This type, reinforced with carbon fibres, has a density of around 1.30–1.40 g/cm³. Known for its high strength-to-weight ratio and electrical conductivity, carbon-filled nylon is commonly used in lightweight, structural, or conductive applications like drone frames and electronic casings.
- Nylon 11 and 12: These nylons have lower densities, about 1.01–1.02 g/cm³, making them lighter than other types. They also offer excellent flexibility and resistance to moisture, making them suitable for harsh environments, such as fuel lines and pneumatic tubing.
Each type of nylon’s density influences its mechanical properties and performance in specific applications. Selecting the suitable nylon based on density can ensure optimal functionality, durability, and efficiency.
Factors Affecting Nylon Density
While different types of nylon have characteristic densities, certain factors can influence the final density of a nylon product. Here are the key factors:
- Crystallinity: Nylon’s molecular structure affects its density. A higher level of crystallinity, where molecules are tightly aligned, increases density and typically enhances strength and thermal stability. Factors like cooling rate, use of nucleating agents, and polymerization methods impact crystallinity. For example, ring-opening polymerization generally results in higher crystallinity than condensation polymerization.
- Polymerization Level: The degree of polymerization, or chain length, impacts nylon’s density. Longer polymer chains tend to produce denser materials. Variables such as molecular weight and reaction conditions during polymerization influence chain length and density.
- Processing Conditions: Manufacturing conditions, including temperature, pressure, and cooling rate, also affect nylon’s density. Higher temperatures may reduce density by causing material expansion, whereas high pressure can compress the material, increasing density. Careful control of these factors is essential in maintaining consistency in nylon properties.
Why Nylon Density Matters in Injection Molding
In plastic injection moulding, a material’s density is critical because it affects how it behaves during the moulding process and in its end use.
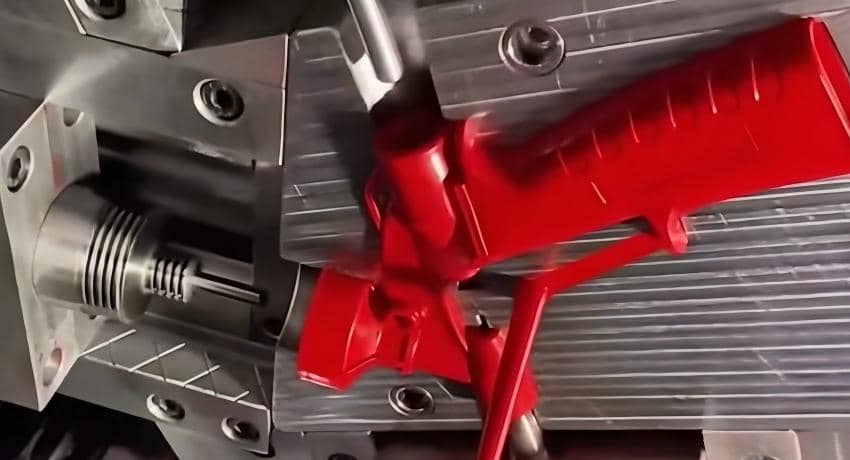
- Flow and Filling: Higher-density nylons may require different injection speeds and pressures to fill moulds correctly. On the other hand, low-density nylons can flow more efficiently, reducing cycle times in some cases.
- Shrinkage and Warping: Materials with higher crystallinity and density may exhibit less shrinkage, leading to more accurate parts with better dimensional stability.
- Weight and Strength: Dense nylons offer greater strength and durability and increase the final product’s weight. Choosing a lower-density nylon can help reduce weight without sacrificing performance in specific applications.
- Thermal Stability: High-density nylons tend to withstand higher temperatures, making them more suitable for applications exposed to heat, like electrical components or automotive parts.
Comparing Nylon Density to Other Materials
Nylon’s density, generally between 1.01 and 1.50 g/cm³, makes it denser than many other plastics but lighter than metals. This balance makes nylon an excellent replacement for metals in applications where weight reduction is beneficial. Here’s a quick comparison:
- Water: Nylon has a density of 1 g/cm³. It sinks in water, making it useful in applications requiring submersion, such as fishing nets.
- Polyethylene (PE): Around 0.91–0.96 g/cm³ density. PE is lighter and has different mechanical properties, so it is often used for flexible packaging.
- Aluminium: Density of 2.70 g/cm³. While much denser than nylon, aluminium is often used in similar applications where strength and lightweight properties are needed, though at a higher cost.