Precision Tractor Fenders for a Customized Solution”
At DSW, we specialize in the precision manufacturing of high-quality press dies and stamped components, including steel tractor and trailer fenders for a variety of industries. Recently, we successfully completed a project for an international client who required custom steel tractor fenders for agricultural machinery. This project demonstrated our expertise in providing comprehensive, end-to-end manufacturing solutions, from initial design through to final delivery, underscoring our commitment to meeting the complex needs of our customers.
2000 Tons for 1+1 cavities Die
Precison Fenders
Hydraulic presses are vital for the production of agricultural tractor fenders.
1. Customer Requirements
Our customer, a professional engineering firm, approached us with precise specifications for their agricultural tractors. They required:
- Durability: The fenders needed to withstand harsh environments, including rough terrains and extreme weather.
- Material: DC06, a cold-rolled steel grade suitable for the most demanding forming processes. This high-quality, low-carbon Ti-alloy IF steel is ideal for complex deep-drawn and stretch-formed parts, such as tractor fenders.
- Size: The fenders, designed for rear tires of small tractors, had dimensions of 1.2mm in thickness and required mold sizes of approximately 2300x1500x1000 mm.
- Custom Design: Each fender required tailored dimensions and mounting points for seamless integration with the tractor’s structure, with CAD drawings provided for both the left and right fenders.
- High Standards: The fenders needed to meet international benchmarks for strength, corrosion resistance, and surface finish.
2. Design and Engineering Phase
Our collaboration began with a detailed consultation to ensure we fully understood the customer’s goals. Working from their 3D drawings, we designed precise die construction and engineering plans that included:
- Reinforced Curves: To increase structural integrity and extend the fenders’ lifespan.
- Optimized Mounting Holes: Ensuring easy installation without requiring additional modifications.
- Anti-Corrosion Coating: Specifying finishes that would protect the steel from rust and wear in harsh agricultural environments.
The design process also involved prototyping and iterative feedback to ensure all specifications were met.
The Importance of Die Design in High-Quality
High-quality tractor fender or trailer fender begin with thoughtful and precise design. From product design to die design, attention to detail ensures the final product meets or exceeds industry standards. Product design focuses on functionality, aesthetics, and real-world performance, while die design ensures accuracy, durability, and consistency. The combination of skilled design and advanced manufacturing techniques delivers reliable, long-lasting, and high-performance tractor fenders or trailer fenders.
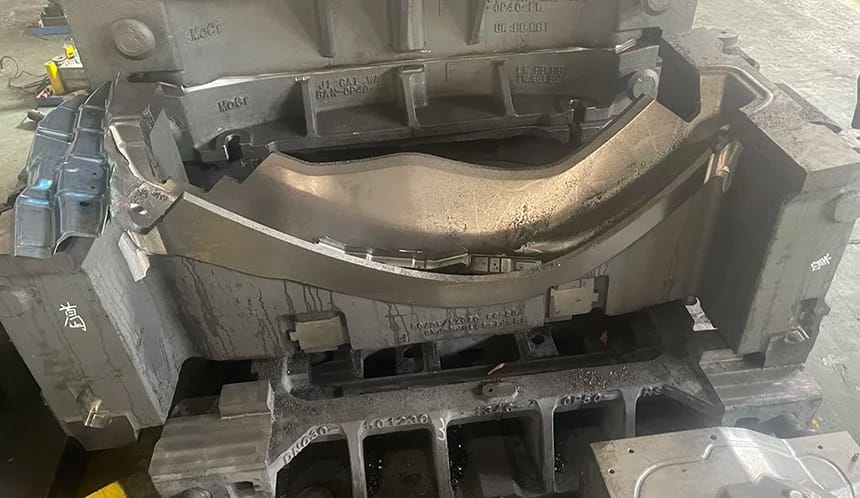
3.Press Dies Design and Process Overview
The following table outlines the different processes used in the design of press dies for manufacturing tractor fenders, including their respective die sizes (Length, Width, and Height):
Process Code | Process | Die Size (L x W x H, mm) |
OP10 | DR (Deep Drawing) | 2500 x 1200 x 950 |
OP20 | CTR (Cutting and Trimming) | 2500 x 1400 x 950 |
OP30 | CTR + CPI (Cutting, Trimming, Coining, and Piercing) | 2350 x 1400 x 950 |
OP40 | FL + RST (Flanging and Reshaping) | 2300 x 950 x 950 |
OP50 | CRST (Crash Forming + Restraining) | 2300 x 1400 x 950 |
OP60 | CPI (Coining and Piercing) | 2150 x 850 x 950 |
Explanation of Processes:
- DR (Deep Drawing): Involves stretching sheet metal into the desired shape, typically for hollow or complex geometries.
- CTR (Cutting and Trimming): Refines the shape by cutting off excess material or trimming deformed edges.
- CPI (Coining and Piercing): Coining involves high-pressure forming to refine areas for precision, while piercing involves punching holes for functional requirements such as bolt or ventilation holes.
- FL + RST (Flanging and Reshaping): Flanging bends the edges of the material to a specific angle, while reshaping ensures that the final design is achieved after previous processes.
- CRST (Crash Forming + Restraining): A combination of rapid forming (Crash Forming) and material stabilization (Restraining) to achieve high-precision parts.
These processes and die sizes represent the careful planning and design required for producing high-quality press components. Each step is crucial to ensuring the accuracy, durability, and performance of the final product.
Materials for Press Dies
- Tool Steel: Known for exceptional hardness, toughness, and wear resistance. Key types include:
- HSS (High-Speed Steel): Ideal for precision cutting at high temperatures.
- Cold Work Tool Steel: Used for forming at room temperature.
- Hot Work Tool Steel: Designed for high-temperature applications.
- Casting Steel: A cost-effective alternative for specific applications.
- Carbide: Highly wear-resistant and suitable for high-volume operations, though more brittle under impact.
- Stainless Steel: Offers superior corrosion resistance, making it ideal for harsh environments.
- Alloy Steels: Provide enhanced strength, toughness, and wear resistance, suitable for complex and large dies.
First Press Die Testing (T1 Sampling) Process
First die testing, or T1 sampling, is a crucial step in the die manufacturing process, designed to validate the die’s performance and ensure that it meets design specifications prior to mass production. The process involves several key steps:
- Initial Pressing and Sample Collection: The die undergoes its first press, producing a pilot batch of samples. The initial 20 pieces are discarded to eliminate any inconsistencies in the early stage of the die’s operation and stabilize the process.
- Dimensional Measurement and Evaluation: The next 20 samples are measured against design specifications. Any deviations in dimensions, shape, or alignment are carefully analyzed to identify the root cause of discrepancies.
- Issue Identification and Die Modification: Upon detecting dimensional variations, the team investigates potential causes, such as tool misalignment, material inconsistencies, or process conditions. Necessary modifications are made to the die, tooling setup, or operational parameters to correct these issues.
- Second Trial: Following die adjustments, a second trial is performed to produce another set of samples. This iterative approach continues until the die consistently produces parts that meet the required specifications.
- Inspection Tooling for Production: To maintain quality in mass production, inspection tooling is employed. This specialized tooling monitors key dimensions during production, allowing for real-time detection of any deviations and ensuring consistency throughout the run.
- Third-Party Quality Control: Independent, third-party inspection services are engaged to provide an unbiased assessment of the die’s performance. These external checks confirm that the parts meet tolerance requirements and objective quality standards, ensuring reliable results free from manufacturer influence.
The T1 sampling process is essential for validating die performance, identifying and correcting potential issues early, and ensuring that mass production runs consistently meet engineering standards. Through this thorough, iterative approach, high-quality parts are produced with minimized risk of defects.
5. Manufacturing Process
Our manufacturing process is optimized for precision and efficiency, consisting of the following key steps:
- Deep Drawing: Utilized for forming processes requiring both pressure and impact, combining toughness and hardness. Cold work tool steels or alloy steels are chosen for their resistance to cracking and deformation.
- Cutting and Shaping: High-precision cutting dies ensured accurate dimensions and clean edges for the fenders.
- Stamping and Pressing: Hydraulic presses were employed to shape the steel sheets with uniformity, achieving consistent results.
- Surface Treatment: To enhance corrosion resistance, sandblasting followed by powder coating was applied, providing a durable, smooth finish.
- Quality Inspection: Each fender underwent comprehensive testing, including dimensional checks, load testing, and visual inspections, to ensure strict adherence to quality standards.
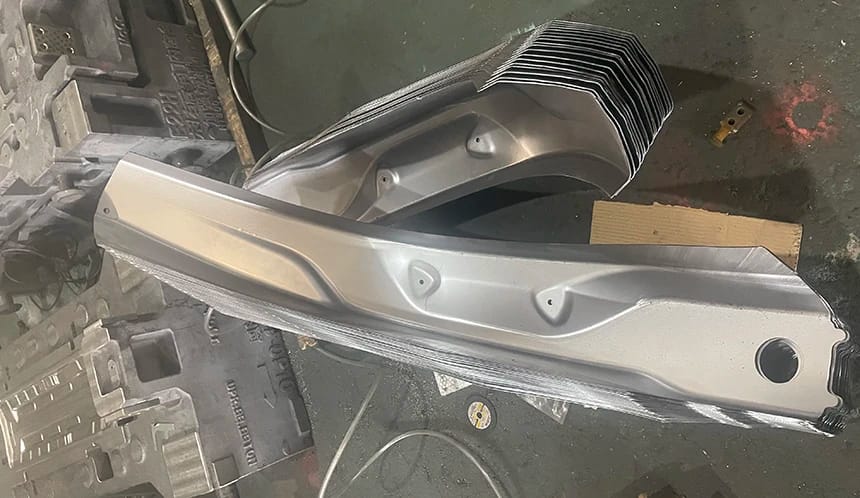
6. Results and Customer Feedback
The final tractor fenders exceeded our customer’s expectations. The key results included:
- Precision Fit: The fenders were custom-tailored to the customer’s tractor models, enabling quick and easy installation.
- Enhanced Durability: Testing confirmed the fenders’ ability to withstand the harsh conditions and heavy workloads they would encounter.
- On-Time Delivery: Despite the complexity of the project, we delivered the fenders on schedule, ensuring the customer’s production timeline remained intact.
The customer expressed high satisfaction with the outcome, praising our professionalism, technical expertise, and commitment to quality.
At DSW, we specialize in manufacturing high-quality press dies, tractor fenders, and trailer fenders for a variety of industries. Our focus is on precise design at every production stage, ensuring that our products not only meet but exceed industry standards. We prioritize functionality, aesthetics, and usability in product design, while our expert die design ensures accuracy, durability, and consistency. With a strong track record in delivering high-quality steel components, we offer tailored solutions to meet the unique needs of our customers. If you need a reliable partner for custom fenders, contact us today to discuss your project!