Custom Plastic Enclosures
Custom plastic enclosures for electronics are bespoke enclosures made from plastic materials that are specifically designed and manufactured to protect and enclose electronic devices or components.
They are meticulously tailored to meet the unique requirements of the electronic device being enclosed.
The design process of plastic housings for electronics involves utilising computer-aided design (CAD) software. Various prototyping and mass production techniques, such as 3D printing, injection moulding, or blow moulding, are employed based on the electronic device’s size, shape, and specifications and the properties of the chosen plastic material.
ABS (Acrylonitrile Butadiene Styrene): This versatile plastic offers a good balance of strength, impact resistance, and affordability.
Polycarbonate (PC): Known for its exceptional clarity, high impact resistance, and flame retardancy, PC is ideal for demanding applications.
Polypropylene (PP): This lightweight material offers excellent chemical resistance and is well-suited for sterilisation applications.
Other Advanced Plastics: Materials like polyamide (PA), PBT (Polybutylene Terephthalate), or PPS (Polyphenylene Sulfide) might be used for specific applications requiring high temperature or chemical resistance, such as automotive or industrial electronics.
Compared to alternative materials like metal or wood, custom plastic enclosures offer distinct advantages. They are lightweight, durable, and corrosion-resistant, making them highly suitable for safeguarding electronic devices in diverse environments. Plastic materials are also cost-effective to produce and can be molded into intricate shapes, providing versatility in customization. However, it is crucial to consider the specific application requirements when selecting a plastic material, as different types of plastic possess distinct properties that may not be universally suitable.
DSW: Leading the Industry in Custom Plastic Enclosures
As a manufacturer specializing in custom plastic enclosures, DSW stands out for its ability to provide high-quality, durable, and cost-effective solutions for electronics, medical devices, and handheld gadgets. Here’s why DSW is a trusted partner:
- Years of Expertise: Since 2004, DSW has been delivering bespoke plastic enclosures for diverse industries, using cutting-edge techniques to meet customer specifications.
- Customer-Centric Approach: DSW’s commitment to customer satisfaction ensures that each project receives a personalized touch, from the initial design concept to the final delivery.
- Flexible Manufacturing: Whether for small batches or large-scale production, DSW offers the ability to accommodate different volumes without compromising quality or lead times.
- Comprehensive Support: DSW provides full engineering support, offering solutions from prototyping to final mass production, ensuring that your product is designed and produced to exacting standards.
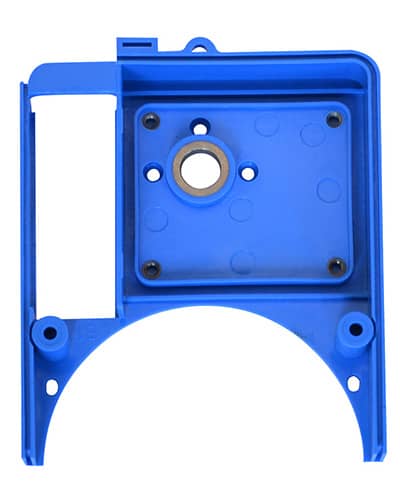
From Design Concept -The Manufacturing Process
To create your custom plastic enclosure for electronics, it is essential to follow a systematic approach that aligns with the size, shape, and requirements of the electronic device, as well as the properties of the plastic material. Here are general steps to consider:
Determine the specific needs of the electronic device and its operating environment to select an appropriate plastic material and design the enclosure accordingly.
Utilize computer-aided design (CAD) software to develop a detailed 3D model of the custom plastic enclosure, enabling visualization and iterative design changes.
Produce a prototype or mock-up of the custom plastic enclosure utilizing prototyping techniques like 3D printing or injection molding. This step allows for testing, refining the fit and functionality, and making necessary adjustments.
Employ a mass production process, such as injection molding, to manufacture the final custom plastic enclosure.
Assemble the custom plastic enclosure according to the design and any additional specifications.
Conduct thorough testing of the final custom plastic enclosure to ensure it meets all requirements and is ready for deployment.
Types of Custom Plastic Enclosures for Specific Applications
Depending on the application, custom plastic enclosures may need to meet specific standards:
- Outdoor Enclosures: Enclosures for devices used outdoors need UV-resistant plastics and IP-rated protection against water and dust (e.g., IP65 or IP67).
- Medical Enclosures: Medical device enclosures need to be biocompatible, easy to clean, and resistant to sterilization processes (e.g., autoclaving).
- Industrial Enclosures: For industrial applications, enclosures must often be resistant to chemicals, oils, and extreme temperatures.
- Consumer Electronics: Enclosures for devices like smartphones, tablets, and other gadgets need to be ergonomic, aesthetically pleasing, and easy to assemble.
- Automotive Enclosures:Automotive enclosures need to withstand harsh conditions inside vehicles, including vibrations, temperature extremes, and exposure to automotive fluids. They must also comply with industry standards for safety and functionality.
Challenges in Custom Plastic Enclosure Design
When designing custom plastic enclosures, several challenges must be considered:
- Complexity of Design: Balancing functionality with aesthetics while ensuring the device fits within the enclosure can be a complex task.
- Environmental Factors: Outdoor and industrial applications require additional considerations for UV stability, waterproofing, and durability.
- Heat Management: Electronic devices can generate significant heat, requiring the enclosure to incorporate proper cooling mechanisms, such as vents or heat sinks.
The Importance of Custom Plastic Enclosures
Custom plastic enclosures play a critical role in the electronics industry, providing a tailored solution for protecting delicate components. From their meticulously designed creation process to the diverse material options, these enclosures offer a lightweight, durable, and cost-effective approach to safeguarding electronic devices across a wide range of applications.
No comment