Why Die Spotting Presses are Essential for Manufacturers and Mold/Die Makers
From the cars we drive to the electronics we use daily, precision molds and dies form the backbone of countless products. At the heart of this precision lies an unsung hero: the die spotting press. These machines are indispensable tools for mold and die makers, ensuring alignment, accuracy, and efficiency in production while driving innovation and quality.
For Exceptional Accuracy
Flawless Precision
Hydraulic die spotting presses are vital for both mold manufacturing and die-casting die production.
Achieving Flawless Precision with Die Spotting Presses
Precision is everything in manufacturing. Even a minor misalignment between mold or die halves can lead to defective products, wasted materials, and costly delays. Die spotting presses solve this problem by ensuring perfect alignment of components, delivering accurate cavities and flawless products. This precision reduces waste, minimizes rework, and improves profitability—a trifecta of benefits for any manufacturer.
What is mold spotting?
Mold spotting—also referred to as mold verification or mold fitting—is the process of making sure all sides of a mold line up exactly. It entails pressing to seal the mold and looking over the contact surfaces for gaps, misalignment, or incorrect seating.
The Key Advantages of Die Spotting Presses
Die spotting presses offer a range of advantages, making them a cornerstone of modern manufacturing:
- Speed and Efficiency:
- These presses streamline production by reducing the time needed for alignment and testing. Faster turnaround times help manufacturers meet tight deadlines and stay competitive.
- Enhanced Safety:
- With advanced safety features, die spotting presses protect operators while maintaining high levels of productivity.
- Unparalleled Precision:
- Exceptional accuracy ensures consistent product quality, reducing defects and material waste.
- Versatility:
- Designed to handle diverse molds and dies, these machines are widely used in industries like automotive, aerospace, and electronics.
Extending Mold and Die Life Through Maintenance and Repair
Die spotting presses play a crucial role in mold and die maintenance. Proper upkeep ensures molds and dies remain reliable and extend their service life, reducing costly disruptions. These machines support several maintenance tasks:
- Inspection: Components are securely mounted on the press for thorough damage assessment.
- Alignment Verification: Dimensional accuracy is checked to maintain tight tolerances.
- Spotting and Fitting: Components are tested and adjusted to ensure seamless functionality.
- Surface Finishing: Controlled pressure corrects imperfections for smooth finishes.
- Welding and Repair: Components are stabilized during complex repair processes.
- Testing and Verification: The accuracy and functionality of dies are confirmed post-repair.
- Preservation and Storage: Disassembled dies are safely packaged to prevent damage.
By facilitating these processes, die spotting presses help minimize downtime, optimize performance, and extend the lifespan of molds and dies.
Hydraulic Die Spotting Presses in Mold and Die-Casting Manufacturing
Hydraulic die-spotting presses are vital for both mold manufacturing and die-casting die production. While both processes demand precision, their requirements differ significantly:
Mold Manufacturing
Mold manufacturing involves crafting tools to shape materials like plastics and metals. Commonly used in industries such as automotive and electronics, this process demands:
- Material Flexibility: Molds must accommodate thermoplastics or thermosetting plastics.
- Tight Tolerances: High dimensional accuracy is essential for intricate details.
- Surface Finishing: Polished surfaces ensure smooth product finishes.
Die spotting presses streamline this process by ensuring alignment, reducing misfits, and improving surface quality during the trial phase.
Die-Casting Die Manufacturing
Die-casting dies are designed to cast metals like aluminum, magnesium, and zinc under extreme conditions. This process requires:
- High Thermal Resistance: Materials like H13 steel are used to withstand intense heat.
- Complex Cooling Systems: Efficient heat dissipation extends die life.
- Durability: Dies must endure high production volumes and thermal cycling.
Die spotting presses optimize die-casting by ensuring precise alignment, fitting, and inspection. This minimizes defects like porosity or incomplete fills, resulting in higher-quality castings.
A Comparison of Applications
The distinctions between mold and die-casting die production influence how die spotting presses are utilized:
Aspect | Mold Manufacturing | Die-Casting Die Manufacturing |
Alignment | Prevent parting line mismatches | Maintain tolerances under high-pressure conditions |
Material Testing | Test with plastic resins | Conduct trial castings with molten metals |
Surface Treatment | Focus on polishing and texturing | Require heat-resistant treatments |
Maintenance and Repair | Adjustments like grinding or polishing | Welding or re-machining with secure press support |
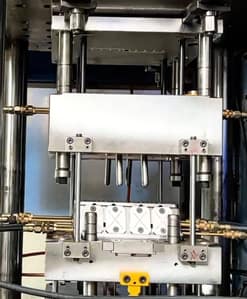
Best Methods for Mold Spotting
Ensuring the accuracy, use, and lifetime of plastic injection molds and die casting molds depends critically on mold spotting. Correct spotting methods enable the identification of dimensional discrepancies, surface flaws, and misalignments that could affect the finished good.
Importantance for Mold Spotting
1. Employ a precision spotting press
Simulate actual molding conditions using spotting presses with precise pressure control. Ensure the press table is level and impurity-free to eliminate skewing findings.
2. Apply surface inspection spotting ink
Reveal contact locations with a high-contrast spotting ink or die-checking paste. Apply a thin, equal coating to prevent too much material from influencing outcomes. Under regulated pressure, close the mold and examine the ink transfer patterns at both high- and low-contact locations.
3. Perform a complete tactile and visual inspection
Search for unequal pressure marks suggesting incorrect mating or alignment. Measure gaps between mold halves using feeler gauges; fix them as necessary. Look at essential places like ejector pin positions, parting lines, and cavity margins.
4. Check for alignment and parallelism
Using dial indicators or laser measurement instruments, guarantee that mold plates and inserts run parallel. Check leader pins, bushings, and guide pins for wear and correct alignment. If you find misalignment, adjust the mold components to achieve an even closure.
5. Streamline surface finishing and venting Check vent sites to avoid trapped air, which could lead to burning marks and short shots in plastic molding. Polish the mating surfaces to the desired finish for proper sealing without too much strain.
6. Attend to issues of thermal expansion
When needed, account for material expansion via hot spotting once the mold reaches its running temperature, and review alignment and contact patterns.
7. Execute tests and corrections
Test shots with the mold in the die casting or injection machine. Review flash, short shots, warping, and other flaws in component quality. The actual molding circumstances determine the final details.
8. Preserve and Record Spotting Notes
Record meticulously the findings of mold spotting, including measurements and ink transfer photos. Plan regular maintenance to look for deviations and wear. Teach and train molders to regularly follow top standards for spotting.
Finally Good mold spotting guarantees correct mold performance, lowers flaws, and increases mold life span. These best practices can help manufacturers lower downtime related to incorrect fitting or mold alignment and raise product quality. Achieving the best mold spotting outcomes depends mostly on regular inspection, accurate equipment, and qualified staff.
The Future of Die Spotting Presses
As manufacturing evolves, die spotting presses are adapting to meet new challenges. Emerging technologies like automation and artificial intelligence (AI) are transforming these machines:
- Predictive Maintenance: AI analyzes wear patterns, scheduling repairs before breakdowns occur.
- Enhanced Precision: Automated adjustments minimize human error, ensuring higher accuracy.
- Remote Operation: Connectivity enables operators to control presses from anywhere, boosting productivity.
By integrating these advancements, manufacturers can stay ahead in an increasingly competitive landscape.
Conclusion
Die spotting presses are indispensable for mold and die makers. They ensure unparalleled precision, efficiency, and safety, driving quality and productivity across industries. Whether aligning components, facilitating maintenance, or adopting future-ready technologies, these machines empower manufacturers to overcome challenges and achieve success. Investing in advanced die spotting presses is not just a smart decision—it’s essential for staying competitive in today’s fast-paced world.