FEEL FREE TO ASK US
MOLD SPECIFICATION IN DETAILS
In the world of manufacturing, precision is paramount. When it comes to producing plastic and metal parts, molds play a crucial role in achieving the desired accuracy and consistency. To procure the right mold for your project, it’s essential to draft a Request for Quotation (RFQ) that contains detailed and precise mold specifications.
- Quality
- Accuracy
- Safety
- Reliance
GENERAL QUESTIONS
Frequently asked questions
- Mold Specifications:
- Type of mold (e.g., injection, blow, compression or die casting).
- Size, dimensions, and complexity of the part(s) to be molded.
- Any special features or custom requirements for the mold.
- Material Requirements:
- Specify the material(s) to be used for the parts.
- Different materials may require specific design considerations.
- Quantity and Lead Time:
- Indicate the number of parts you need to produce.
- Provide the required lead time for mold production.
Germany, China, the United States, Japan, Italy, and Brazil are nations wherein the mould-making industry extensively utilizes HASCO components. These countries possess substantial sectors dedicated to mould-making and have enthusiastically adopted HASCO’s standardized mould components to enhance their manufacturing processes.
It is crucial to acknowledge that although HASCO enjoys popularity in Europe and DME in North America and Canada, its applicability is not limited exclusively to these regions. In reality, HASCO and DME standard mold components have garnered users and market share globally, finding wide-ranging utilization in various other areas and countries.
Tight tolerances are critical in the medical industry as they ensure that the part functions as intended. Some elements of the injection molding process that can impact tolerance control include:
Size and design of the plastic part — Characteristics such as wall thickness, draft angles, and overall product size can all have significant impact on tolerances. Expertise in injection molding is required to avoid product defects, warpage, shrinkage, void areas, and splitting or cracks.
Material selection — Selecting the right material for your specific application is critical. The various types of plastics used in injection molding are all unique in their chemical and physical properties. Therefore, some materials will work much better under certain conditions than others. Choosing a manufacturing partner with knowledge and experience can help you find the right material for your needs.
Tooling — Decisions such as gate and cooling channel placement, along with injection pressure, melting temperature, and ejection pin location are all essential for ensuring the quality of the end-product. Collaborating with a partner who understands the importance of these decisions is vital.
Consistent process controls — Sometimes, after the first few batches are made in full-production, minor tweaks need to be made to the manufacturing process (such as altering temperature, holding times, and pressure) in order to optimize efficiency. Once this is done, it’s important to utilize tools like sensors and other feedback methods to ensure that these parameters remain consistent throughout production.
A mold is typically used for plastic or composite materials, shaping molten or softened material into a specific form. A die refers to tools for stamping or die-casting metals, where the material is shaped by cutting or casting.
The lifespan of a mold depends on the material used, the number of cycles, and how well it’s maintained. For example, P20 molds may last between 50,000 and 100,000 cycles, while higher-end steels like H13 or 718 can endure 200,000 cycles or more.
TECHNICAL QUESTIONS
Frequently asked questions
Selecting the right mold steel depends on factors such as:
- Type of Material Being Molded: Some plastics and metals require higher wear and corrosion resistance.
- Production Volume: High-volume production requires steels with higher hardness and durability.
- Surface Finish Requirements: Steels like S136 or NAK80 are preferred for applications needing high polish, such as optical or cosmetic parts.
- Operating Environment: Corrosive or high-humidity environments benefit from stainless steel options like S136.
Standard mold steels are specially treated steels used in mold-making for injection molding, die casting, and other manufacturing processes. These steels must be durable, heat-resistant, and withstand repetitive cycles. Here are some commonly used mold steels:
- P20 Steel: Pre-hardened, durable, and wear-resistant; ideal for general-purpose injection molds.
- 718 Steel: Modified P20 with added nickel for toughness and corrosion resistance; used for larger, high-precision molds.
- S136 Steel: Stainless steel with excellent corrosion resistance and polishability; used for medical or food-grade molds.
- H13 Steel: Heat-resistant, tough, and resistant to thermal fatigue; commonly used in die casting and high-temperature plastic molds.
- NAK80 Steel: Pre-hardened, with excellent machinability and polishability; used for intricate mold designs and cosmetic applications.
- 2344 Steel: Similar to H13 with enhanced thermal fatigue resistance; used for aluminium and magnesium die-casting moulds.
- 45# Steel: Medium-carbon steel for mold bases, offering good strength but limited wear resistance.
H-13 Steel stands out as an exceptional choice. This type of steel is specifically designed and manufactured to withstand wear, thermal fatigue, and extreme temperatures. With its remarkable properties, H-13 Steel surpasses other materials like P-20 Steel, particularly in applications requiring deep cavity molds and prolonged exposure to intense heat.
The utilization of H-13 Steel in hot work tooling and high-heat applications is a testament to its exceptional characteristics. Its hardness, resistance to wear and thermal fatigue, and suitability for deep cavity molds make it the material of choice for demanding manufacturing processes.
Tolerances depend on the material and process but typically range from ±0.05 mm to ±0.1 mm for most parts.
A draft angle of 1° to 3° per side is standard for easy part ejection. Higher draft angles may be needed for deeper cavities.
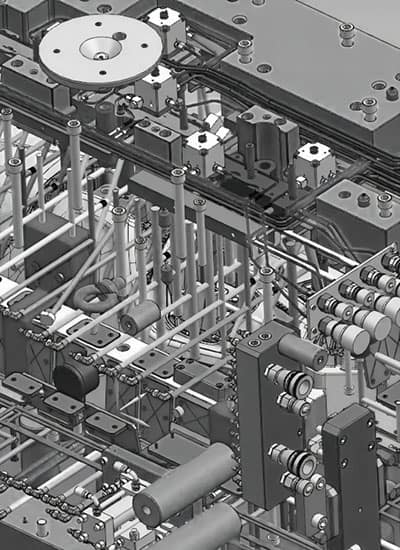
Ask Us
Quick contact form