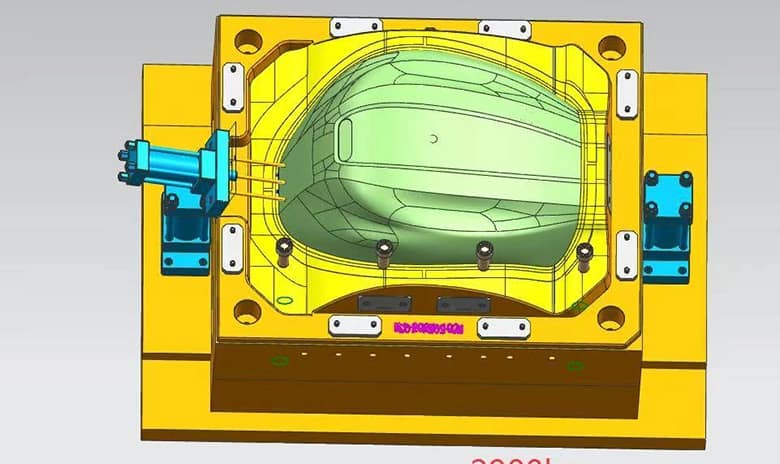
Two common types of molds are used in plastic injection molding: insert molds and free stand molds. Each type offers unique benefits and applications, depending on the project’s specific needs. Understanding the differences between these two mold types can help manufacturers make the right choice for their plastic injection molding processes.
What is a Free Stand Mold?
Simple Design, Minimal Slides, No Core Mechanism
A free-standing mold (or stand-alone mold) does not incorporate additional inserts or mechanical features, such as core pins or cavities, which would demand intricate mold components to function. Instead, it relies solely on the shape of the mold cavity to produce the part. Free-standing molds create simpler plastic components without the need for additional reinforcement or complex internal mechanisms, such as threaded holes or inserts. It’s straightforward to say that the mold core and mold cavities integrate with A and B plates, using the same mold steel.
Key Features of Standalone Mold
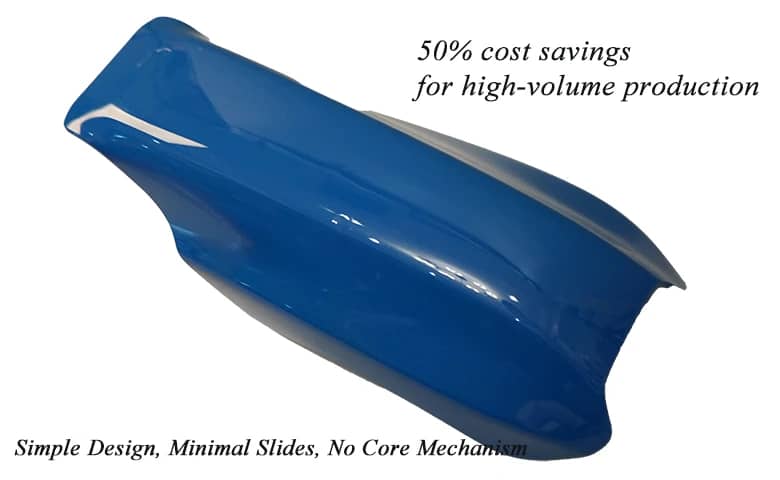
1. No Inserts Required: Unlike insert molds, free-stand molds do not involve placing any pre-formed components in the mold cavity.
2. Simpler Process: The process is generally simpler and faster as it involves only the plastic injection without the need for placing and securing inserts.
3. Versatile for Many Products: Free-stand molds are suitable for a wide range of applications, especially when parts are purely made of plastic without any metal or complex integration.
What is an Insert Mold?
Complex Design, Integrated Inserts, High-Precision Parts
An insert mold is a type of mold in which a pre-formed component, typically a metal insert, is placed into the mold cavity before the plastic is injected. This process allows for the combination of plastic and metal components in a single molded part. Insert molding is often used in applications where added strength, electrical conductivity, or a mechanical feature is needed.
Key Features of Insert Mold
1. Use of Inserts: The key characteristic of insert molding is that it involves placing inserts (usually metal) into the mold cavity, which are then surrounded by molten plastic.
2. Enhanced Strength and Functionality: The inserts help provide additional strength, stability, and functionality, such as threads or electrical contacts.
3. Cost-Efficient for Certain Applications: For parts requiring metal components (e.g., screws, pins), insert molding eliminates the need for separate assembly processes, making it cost-effective.
Comparing Insert Mould vs. Free-Stand Mould
Complexity:
Insert Mold: More complex due to the necessity of pre-inserted components, often requiring additional steps for insert placement and secure handling.
Free-Stand Mould: Simpler and quicker, as it involves only the injection of plastic into the cavity.
Applications:
Insert Mold: Ideal for producing parts with embedded metal features, such as threaded inserts, electrical connectors, and high-strength parts.
Free-Standing Mold: Best suited for parts that are entirely plastic and do not necessitate metal inserts, such as housings, enclosures, and basic components.
Cost:
Insert Mould: While more complex, the elimination of additional assembly processes can reduce long-term costs in specific applications.
Free-Standing Mold: Typically less expensive due to the simpler process, but may not be suitable for parts requiring metal features, which could increase overall costs if done separately.
Material Flexibility:
Insert Mould: Provides greater material flexibility, allowing the combination of different materials, such as plastic and metal, in one part.
Free-Stand Mould: Limited to using a single material—usually plastic—throughout the entire part.
Part Strength:
Insert Mould: Produces stronger and more durable parts, particularly when metal inserts are used, as they enhance mechanical properties.
Free-Standing Mold: Generally, parts made from free-standing molds may not exhibit the same strength as those with integrated metal components.
Customization:
Insert Mould: Offers high customization, especially in producing parts that require specific mechanical functions, such as threaded holes or electrical connectors.
Free-Stand Mould: While customizable in terms of shape and design, it doesn’t afford the same level of mechanical customization as insert moulding.
Half the Cost, Longer Lifespan
Perfect for high-volume production of cost-effective plastic parts – get in touch with us.
The Lifespan of Mold Tooling
The shot quantity refers to the number of parts that can be produced per cycle or shot of the injection molding machine. This varies based on the mold design, including whether it’s an insert mold or free-stand mold. Here’s how the shot quantity typically compares between the two:
Insert Mold
- Shot Quantity: Generally, the shot quantity in insert molds tends to be lower than in free-stand molds. This is because insert molding involves additional steps like placing metal inserts or components into the mold cavity before injecting the plastic.
- Factors: The shot quantity can depend on:
- The complexity of the insert placement.
- The number of inserts required in each part.
- The type and size of the insert.
- The need for additional cooling or curing processes.
- Typical Use: Insert molding is often used for parts with metal components or specific features, such as threaded inserts, which require more precise handling, and this can reduce the overall shot quantity per cycle.
Free-Stand Mold
- Shot Quantity: Free-stand molds typically allow for higher shot quantities because they involve only the injection of plastic into the mold cavity without the need for insert placement.
- Factors: The quantity can be influenced by:
- The complexity of the mold design.
- The number of cavities in the mold.
- The type of plastic material used.
- Typical Use: Free-stand molding is more straightforward, making it ideal for mass production of plastic parts in simple construction, and allows for higher shot quantities per cycle.
Applications of Free Stand Molds
Free stand molds are particularly useful in industries that require the production of simple plastic parts in large quantities. Some of the common applications include:
- Consumer Goods: Parts like plastic enclosures, containers, and household products.
- Automotive Industry: Simple plastic components, such as clips, covers, and trims.
- Medical Devices: Molding of basic housings or cases for medical devices.
- Packaging: Containers, lids, and plastic packaging products that do not require complex features.
When Should You Use Free-Standing Molds?
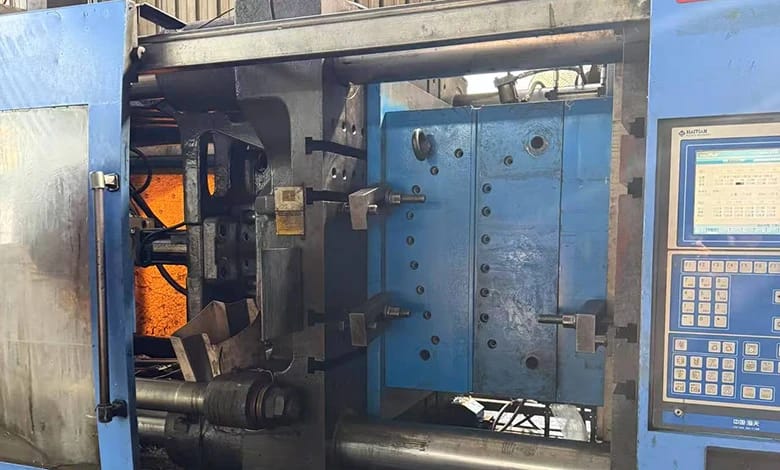
Standalone molds are best used when:
- The produced parts are simple in design and do not require complex features like threads or inserts.
- Cost and speed are critical factors in production.
- The production volume is high, as free-standing molds are particularly efficient for mass production of essential parts.
Simple Plastic Parts refer to plastic components that have basic geometries, minimal functional features, and require little to no additional elements such as inserts, complex mechanisms, or intricate surface textures. These parts are usually easier and faster to design, manufacture, and mold due to their straightforward structure. In the context of plastic mold design, simple plastic parts have characteristics that make them more cost-effective to produce and require less complex mold designs.
Characteristics of Simple Plastic Parts
- Basic Geometries:
- Simple plastic parts often have basic shapes such as rectangular, cylindrical, or spherical designs. These parts don’t involve complex curves, deep pockets, or unusual angles.
- Examples include flat panels, covers, enclosures, trays, and basic containers.
- No Inserts or Complex Components:
- These parts typically do not require the inclusion of metal inserts, threaded holes, or any other secondary components that need additional tooling or handling during the molding process.
- They may have holes or slots but are not designed to accommodate complex internal structures like ribs or features requiring additional support.
- Minimal Surface Detail:
- Simple parts tend to have a smooth or lightly textured surface. They don’t require intricate surface patterns or high tolerance finishes.
- Surface treatments are often simple, such as a matte or glossy finish, and do not involve complex decorative features like engraving or embossing.
- Single Material Use:
- Simple parts typically use one type of plastic material without needing multiple materials or overmolding processes.
- Parts are generally uniform throughout the molding process and don’t require additional layers or mixing of materials for functional purposes.
- Standard Tolerances:
- These parts have less stringent tolerance requirements, which means the design can be less intricate and more forgiving during the molding process.
Common Examples of Simple Plastic Parts
- Enclosures for electronic devices or appliances.
- Containers such as lids, trays, or cases for food packaging.
- Housing for non-mechanical devices.
- Plastic caps and covers for various uses.
- Basic automotive components, like clips, trim parts, or bezels.
- Medical device housings without intricate features.