Plastics for Medical Devices and Applications
Ensuring Safety and Longevity with Medical-Grade Plastics
Medical devices are made of various materials. Selection is crucial since it impacts safety, durability, and performance. Selecting the right materials is critical to meeting regulatory standards, ensuring patient safety, and the growing demand for advanced medical technology.
Due to their biocompatibility and unique properties, medical-grade plastics are a significant player in the industry. Therefore, these materials are used in various medical applications and are essential for designing and manufacturing medical devices.
This article provides insight into the various types of medical-grade plastics, their properties, and their applications within the medical industry.
Understanding Medical-Grade Plastics
Medical device manufacturers must adhere to stringent standards, with ISO 10993 and the U.S. Pharmacopeial Convention (USP) pivotal in material selection. However, no definitive list of biocompatible polymers complicates the selection process. Here, we provide an overview of six essential polymers for medical parts.
Critical Properties of Medical-Grade Plastics
Medical-grade plastics must be:
- Resistant to corrosion, chemical attack, and high temperatures
- Non-absorbent and inert
- Capable of withstanding repeated sterilization cycles
- Biocompatible and non-reactive with bodily fluids and tissues
- Strong and durable
- Thermal Stability: Maintains integrity at high temperatures, crucial for sterilization processes.
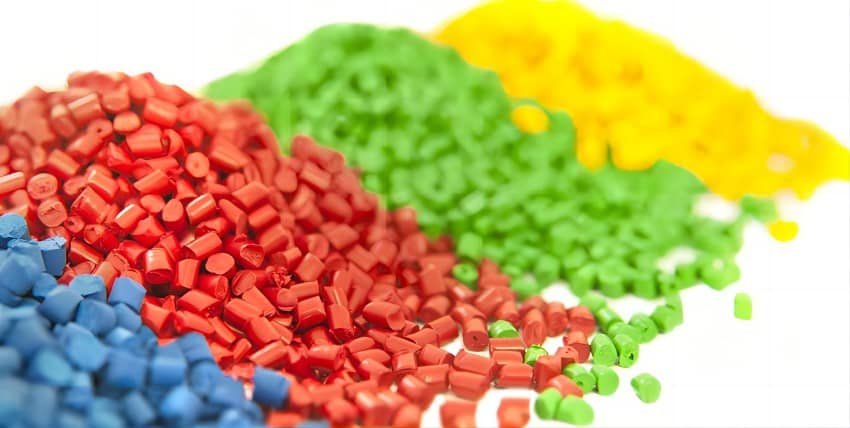
Essential Medical-Grade Plastics
- PEEK (Polyetheretherketone)
- Used in trauma fixation, spinal implants, and dental applications
- Lightweight, strong, and radiopaque
- Biocompatible and sterilizable
- UHMW-PE (Ultra-High Molecular Weight Polyethylene)
- Used in knee and hip replacements
- Dense, low-friction, and impact-resistant
- Biocompatible and suitable for repeated sterilization
- PEI (Polyetherimide)
- Known as Ultem
- Heat-resistant and strong
- Used in surgical instrument handles and medical device enclosures
- PSU (Polysulfone)
- Tough and rigid at high temperatures
- Used in filter housings, catheter ports, and surgical trays
- Can withstand extensive steam sterilization
- PC (Polycarbonate)
- Optically transparent and tough
- Used for blood and drug flow visualization
- Suitable for 3D printing and injection moulding
- Silicone
- Flexible and durable
- Used in prosthetics, seals, and gaskets
- Resistant to extreme temperatures and chemicals
Additional Considerations
Other notable medical-grade plastics include PTFE (Teflon), ABS, acetal, PVC, PET, and PP. Each has unique properties that make them suitable for various medical applications, from catheters to specimen bottles.
Choosing the Right Plastic
Selecting the appropriate medical-grade plastic depends on its physical, chemical, and electrical requirements, manufacturability, and compliance with FDA standards. DSW can assist in navigating this complex landscape, offering expertise in material selection and manufacturing processes.
Advantages of Medical-Grade Plastics
- Versatility: Moldable into different shapes, enhancing innovation in medical technology.
- Easy Sterilization: Compatible with various sterilization methods, reducing contamination risks.
- Infection Resistance: Anti-microbial properties reduce bacteria growth and cross-contamination.
- Cost-Effectiveness: Lower material and manufacturing costs compared to metals and glass.
- Environmental Friendliness: Many medical thermoplastics are recyclable, reducing waste.
Conclusion
Medical-grade plastics play a vital role in the healthcare industry, offering biocompatibility, durability, and versatility. Choosing the suitable plastic is crucial for ensuring the safety and efficacy of medical devices. DSW provides comprehensive support in selecting and manufacturing medical-grade plastics for various applications. Contact us to learn more and get started on your next project.