Plastic Mold Design
Plastic mold design is a critical step in the injection molding process, as it directly impacts the quality, efficiency, and cost-effectiveness of producing plastic parts. A well-designed mold ensures precise production, minimal defects, and high consistency. Whether you’re creating prototypes or full-scale production runs, understanding the types of molds and the design process is essential.
DSW has been offering custom mold design services to the plastics industry since 2004. While we may not be a large company, we bring years of expertise in plastic mold design and custom mold solutions. Additionally, we provide high-quality engineering services to manufacturers across the industry.
At DSW, we have various tooling options available to you, offering different levels of capability from prototype to short pre-production runs to total production quantities.
We can provide you with:
Low volume:-Soft tooling for a few thousand cycles
Medium volume:-P20 (pre-toughened) tooling for up to 20,000
Higher volume:- Fully hardened tooling such as H13 hardened steel in various guises up to 1,000,000 cycles maintenance-free.
Where the cost of several mould tools would be prohibitive, we can offer Family tools that produce more than one component design.
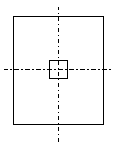
Single Cavity
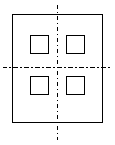
(low volume/low cost) Multi Cavity
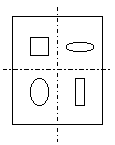
Family Tool (lower tooling cost)
Mold design involves creating a complex assembly of multiple components to produce a specific plastic product.
A typical injection mould structure includes key components: a mold base for support, a cavity and core defining shape, a sprue bushing for material entry, runners and gates for material flow, an ejector system for product removal, a cooling system for solidification, and a venting system for air release.
Features of Cavity Molds
Design Precision: The design of a cavity mold must be highly accurate to ensure the final product meets exact specifications. This includes accounting for shrinkage, parting lines, and draft angles to make it easier to remove the molded part.
Material Strength: Cavity molds are typically made from durable materials like steel or aluminum to withstand the high pressures and temperatures of the injection molding process.
Cooling Systems: Efficient cooling systems are built into cavity molds to rapidly cool the molten plastic, helping to solidify the part and reduce production time.
Surface Finish: The interior surfaces of the cavity mold can be polished or textured to give the final plastic part the desired finish, ranging from high gloss to matte or textured patterns.
Multi-cavity Molds: For high-volume production, multi-cavity molds allow multiple identical parts to be produced in a single injection cycle, increasing productivity and reducing manufacturing costs.
Superior quality: Injection molding produces parts with precise and consistent dimensions.
All are available in Soft or P20 or Fully Hardened tooling
- Total experience in mould design, tool design and manufacture.
- We can tackle the most complex automotive and security components to simple speaker components feet!
- Some customers tap into our expertise for tool design and undertake the manufacture of tooling and plastic components themselves!
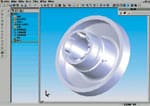
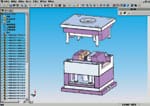
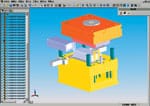
Construction Injection Mold Design
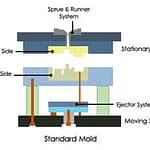
1. Standard Molds
The standard molds are simple to construct. They have two sides: the core side and the cavity side. The cavity side flows plastic material between the nozzle and cavity parts.
Standard molds only have one opening and parting direction. This type is used in plastic parts which do not have an undercut or inner and outer screws.
The ejector pin is shown in light brown and straight.
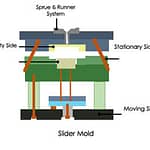
2. Slide mold
This mould has been using slider parts for various types. Basic slide mould transfers horizontal movements of mould to vertical movements. This particular mold variation is particularly useful for producing parts with undercuts, allowing for the creation of intricate geometries and complex features.
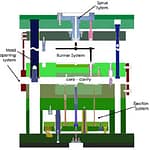
3. Three plate molds
Three-plate molds, characterized by two parting lines and a floating plate supported by support pins, offer a versatile solution for gating flexibility. The presence of two parting planes enables the runner system to be positioned on one side of the floating plate or on a dedicated runner plate that attaches to the floating plate. This additional plate, known as the runner plate, allows for enhanced control over the gating location. The utilization of three-plate molds proves advantageous due to their exceptional flexibility, even when employed for multiple cavity configurations.
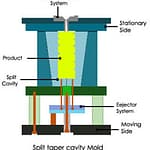
4. Split Cavity Mold
The split cavity is the same as two two-plate standard molds, but the cavity has a split block to make undercut products or external threads. This type of mold is used when the slider is not enough to make the undercut or the threads. The disadvantage of this mold is when used for little parts, the construction will be complex.
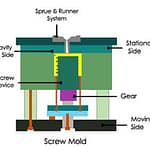
5. Mold With Screw Device
This specialized mold is designed specifically for thread forming applications. It incorporates a rotatable core during the demolding process, allowing for the creation of both internal and external threads. With this mold type, precise and efficient thread formation can be achieved, catering to a wide range of manufacturing needs.
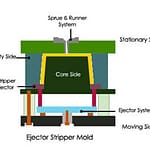
6. Stripper Ejector Mold
This mold type serves the specialized purpose of producing cup-shaped parts without undercuts. Including a stripper ejector facilitates smooth and effortless ejection, ensuring consistent movement and power distribution throughout the product. Moreover, this mold type minimizes the occurrence of unsightly marks on the final product.
Molds with complex and difficult design can be integrated or combined one to the others mold type.
Key Considerations in Mold Design
Material Selection
Molds are typically made from durable materials like steel or aluminum to withstand the high pressures and temperatures involved in injection molding. The choice of material depends on the required production volume, the type of plastic being used, and the desired lifespan of the mold.
Cooling Systems
Efficient cooling is critical for reducing cycle times and ensuring consistent part quality. Mold cooling systems are carefully designed to ensure that the plastic solidifies at the right rate, which is crucial for maintaining part dimensions and preventing defects.
Mold Flow Analysis
Mold flow analysis is a critical step in the design process that simulates the injection molding process. It helps designers identify potential issues such as uneven material distribution, air traps, or incomplete filling. This analysis ensures that the mold design will produce parts with minimal defects and optimal performance.
Ejection Mechanism
The ejection system is responsible for removing the molded part from the mold after it has cooled and solidified. This system can include ejector pins, strippers, or air blasts, depending on the complexity and size of the part.
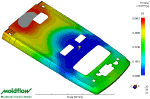
Moldflow Plastic Adviser, Plastics Insight, Moldflow Mpi, Mold Flow Communicator, and Mold Adviser are Mould flow software products for simulating the injection molding of plastic materials. DSW use CAD Connectivity Tools to link structural CAD – CAE to MPI, MPA and MPX Community projects in the plastics and tool-making industry.
After considering the plastic mould design and cost elements, it’s time to mold the plastic. This step is done entirely by the production team. After all, DSW is not only a consulting or injection molding design firm but also a troubleshooter and analysis technician. The moulded plastics production process steps are carefully planned and adhere to industry certification standards. In addition, customers benefit from experienced plastics engineers working on their part. The plastic is cooled and packaged after molding.
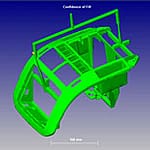
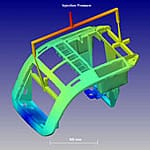
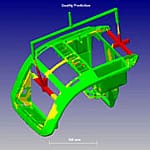
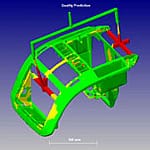
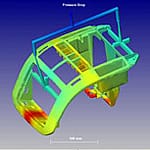
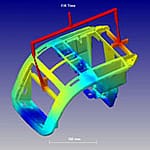
These main components work together in a coordinated manner during the injection molding process to produce high-quality plastic products with the desired shape, features, and surface finish.
The Mold Design Process
- Conceptualization and Design
The first step in mold design is conceptualizing the part’s design and determining the necessary mold type. This involves assessing the product’s geometry, functionality, and material requirements. - CAD Modeling
Once the design concept is established, a 3D model is created using CAD software. This model provides detailed visualizations of the mold, including the core, cavity, cooling channels, and ejection mechanisms. - Mold Flow Simulation
Mold flow analysis software is used to simulate the injection molding process. This helps identify any potential issues with material flow, cooling, or part ejection before production begins. - Tooling and Fabrication
After the mold design is finalized, tooling is created based on the CAD model. The tooling process involves machining the mold components from durable materials and ensuring that the mold is assembled correctly. - Testing and Iteration
Once the mold is fabricated, it undergoes testing to ensure that it produces high-quality parts. Any necessary adjustments are made to optimize the mold’s performance, such as refining cooling channels or adjusting the ejection system.
Expertise in Plastic Mold Design
At DSW, we bring over 20 years of experience in custom mold design and manufacturing. Our team works closely with clients to create molds that meet their exact specifications, whether they require low-volume production or high-volume solutions. We offer a wide range of tooling options, from soft tooling for prototypes to fully hardened molds for mass production, ensuring that we can meet the diverse needs of our customers.
Our design services include mold flow analysis, CAD modeling, and engineering support throughout the production process. We’re equipped to handle both simple and complex mold designs for various industries, from automotive components to consumer electronics.
Conclusion
Plastic mold design is a complex yet critical aspect of the injection moulding process, influencing everything from part quality to production efficiency. By understanding the different types of molds, materials, and design considerations, manufacturers can optimize their production processes and ensure high-quality output. Whether you’re looking for a single-cavity mold or a more advanced multi-cavity or family mold, DSW offers tailored solutions to meet your needs.
No comment