PLASTIC INJECTION MOLD
From design and prototyping to mold creation and production
DSW is an ISO 9001:2018-certified plastic injection mold manufacturer dedicated to meeting high quality and regulatory standards. Our quality assurance processes ensure that all molds & toolings are delivered on time and defect-free.
From our administrative staff to operators and engineers, quality is ingrained in our company culture. We follow industry best practices and invest in advanced technologies to ensure consistent product excellence.
DSW Industry has a 20,000-square-meter mold manufacturing plant specialising in producing plastic parts weighing 2g and 3.5kg. We have delivered almost 10,000 high-quality injection moulds and provided comprehensive plastic injection moulding services to clients worldwide.
The Supplier of Plastic Injection Mold
Manufacturing Custom Plastic Molds
Building custom plastic injection molds involves two primary machining methods: Electrical Discharge Machining (EDM) and Computer Numerical Control (CNC) machining. Each method is essential for creating precise mold components that meet complex design specifications.
EDM Machining
EDM uses a copper or graphite electrode to burn the mold shape into the component. This process is ideal for intricate details like sharp corners or thin ribs that cannot be easily cut with CNC. While slower and more expensive, EDM provides unmatched precision for complex mold features. The steps include:
- CNC machining electrodes from copper or graphite.
- Submerging both the electrode and mold in dielectric fluid.
- Using an EDM machine to discharge electricity at a controlled rate to erode the mold material into the required shape.
CNC Machining
CNC machining utilizes computer-controlled technology to cut precise geometries from raw metal blocks. Designers create 3D CAD models that define the mold’s dimensions, which are then converted into CAM software instructions. The CNC machine follows these instructions to cut the mold with high speed and efficiency. CNC machining is faster and more cost-effective for producing large, less intricate features of the mold.
The combination of EDM for detailed features and CNC for broader shapes ensures high-quality, durable molds capable of producing complex plastic parts.
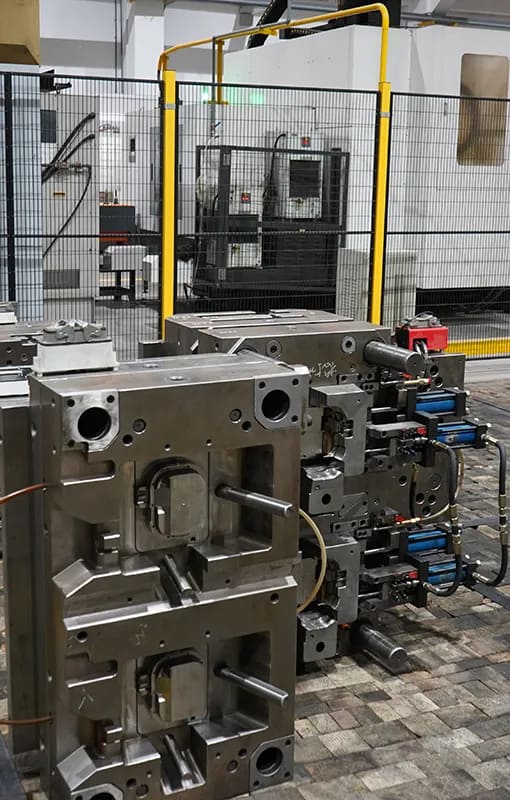
Benefits of Plastic Injection Mold ?
The Department of Buildings promotes the safety build
We provide injection molding solutions to a wide range of industries, delivering high-precision, cost-effective plastic parts for various applications. Our expertise spans across multiple sectors, including:
- High Precision and Consistency: Ensures identical parts with tight tolerances and minimal defects.
- Complex Designs: Capable of producing intricate shapes, detailed geometries, and internal features.
- Cost-Effective for Mass Production: Low per-unit costs for large quantities, with minimal material waste.
- Wide Material Options: Accommodates various thermoplastic and thermosetting materials for different needs.
- Shorter Lead Times: Fast production cycles once the mold is created, ideal for high-demand industries.
- Minimal Waste: Excess material can be recycled, reducing environmental impact.
- Low Labor Costs: Automated process minimizes the need for manual labor.
- Insert Capability: Allows embedding components like metal inserts during the molding process.
- Strong, Durable Parts: Produces lightweight yet strong components for diverse applications.
- Reduced Post-Processing: Smooth surfaces and precise dimensions reduce the need for additional finishing.
Conclusion: Plastic injection molding is efficient, versatile, and cost-effective, making it a preferred choice for industries requiring high-quality, durable parts at scale.
Types of Plastic Injection Mould ?
For automotive, electronics, medical and more
At DSW, we service a wide range of plastic injection molds, including:
- Hot Runner Molds – Heated runner systems to reduce waste and cycle time.
- Two-Plate Molds—Simple molds for single-cavity parts.
- Three-Plate Molds—Molds with an extra plate for separate gating.
- Insert Molds – Molds with pre-inserted metal or plastic components.
- Multi-Cavity Molds—Molds for producing multiple identical parts simultaneously.
- Standalone Mold — Suitable for producing big, less complex parts, or when the production volume doesn’t justify the use of a more advanced, automated mold system.
We provide precise, efficient solutions tailored to meet your manufacturing needs.
Advantages of Molds Made in China
China has become a global hub for mold manufacturing, offering key benefits:
- Cost-Effectiveness: Lower labor and production costs enable competitive pricing for both large-volume orders and complex designs.
- High-Quality Standards: Adherence to strict quality standards, including certifications like ISO 9001, ensures durable, precise molds made from high-quality materials.
- Fast Turnaround: Advanced infrastructure allows for rapid production and delivery, helping meet tight deadlines and reduce lead times.
- Customization and Flexibility: Chinese manufacturers offer a wide range of customizable molds for various industries, including automotive, medical, and electronics.
- Advanced Technology: Access to cutting-edge technologies like CNC machining and 3D printing ensures high precision and efficient production.
- Experienced Workforce: Skilled engineers with extensive experience ensure precise mold design and manufacturing, meeting international standards.
Standards For Injection Mold Components
HASCO, LKM, and DME all offer highly standardized, modular systems for mold components, which ensure compatibility, precision, and cost-effectiveness.
HASCO, LKM, and DME are leading standards for injection mold components:
- HASCO: Modular system, widely used in Europe, offering high precision with customization.
- LKM: Popular in Asia, providing cost-effective, precise components for various industries.
- DME: Known for precision and quality, mainly used in North America.
All are compatible with minor sizing differences.
Tip: By knowing the location of your injection molding facility, we can recommend the most suitable standard for your needs. This ensures you can easily source precise mold parts locally whenever maintenance is required.
Common Mold Steel Optional
The mold steels we commonly use for plastic injection molds in our factory include the following, with many additional options available.
- P20 – General-purpose, pre-hardened steel for medium-volume molds.
- H13 – Heat-resistant steel for high-temperature, high-volume applications.
- S7 – Tough, shock-resistant steel for complex and high-impact molds.
- 420 Stainless Steel – Corrosion-resistant steel, often used for medical and food-grade molds.
- AISI D2 – High wear resistance, used for molds with abrasive plastics.
- NAK80 – High polishability for molds requiring glossy finishes.
- S136 – Corrosion-resistant steel, ideal for food and medical industry molds.
- AISI L2 – Versatile and tough, suitable for impact-resistant applications.
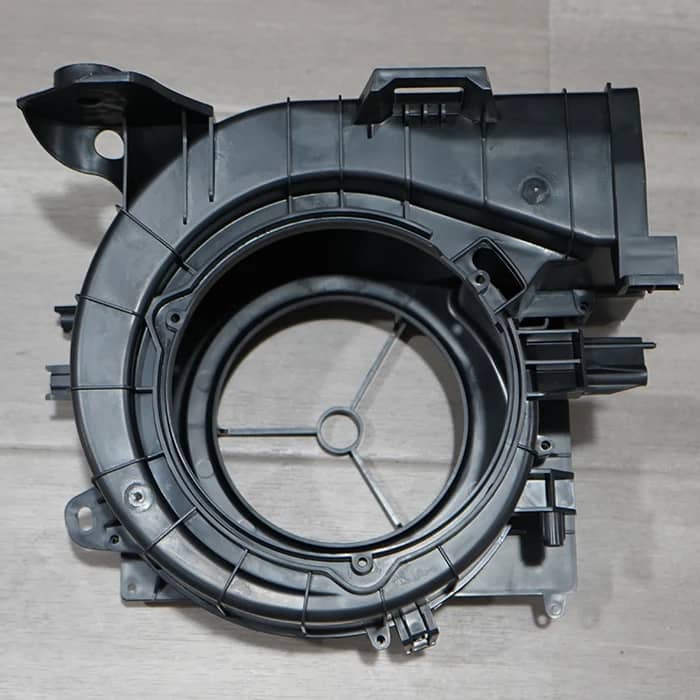
Applications of Injection Molds
Industries We Serve.
All kinds of machines ranging from 90 tons to 2,000 tons for plastic molded parts
Plastic injection molds are essential in various industries for producing complex, high-precision plastic parts efficiently. Key applications include:
- Automotive: Interior/exterior parts, engine components, and functional parts like fuel tanks and gears.
- Electronics: Enclosures for devices, connectors, switches, and circuit board components.
- Medical: Components for medical devices, sterile packaging, and disposable items.
- Consumer Goods: Everyday items like containers, toys, and kitchen appliances.
- Packaging: Bottles, jars, and custom packaging solutions for various products.
- Furniture: Components like chair legs and table parts.
- Aerospace: Lightweight components for aircraft and space technology.
- Industrial: Machinery parts, gearboxes, and tool components.
- Telecommunications: Casings, connectors, and network equipment parts.
- Sports: Equipment parts like golf club heads and bicycle components.
Plastic injection molding offers cost-effective, high-quality solutions across diverse industries, making it a versatile manufacturing process.
Start Your Project Today …
Trust DSW for top-quality custom plastic injection molds, precision machining, and fast turnaround times.