Comprehensive Guide on Polyvinyl Chloride (PVC)
Polyvinyl Chloride (plastic PVC), commonly called vinyl, is one of the world’s most versatile thermoplastic materials used across numerous industries. From construction applications such as pipes and window frames, medical devices, wire insulation and packaging – Plastic PVC has quickly become one of the world’s third-largest synthetic plastic polymers by volume, making it one of the go-to choices due to its durability, affordability and adaptability. We will discuss its key characteristics, various forms produced, and environmental impacts through our comprehensive guide!
What is Polyvinyl Chloride?
Polyvinyl Chloride, often abbreviated as PVC, is a high-strength thermoplastic polymer made from vinyl chloride monomers. It is primarily produced in flexible (plasticised) and rigid (unplasticised), making it suitable for various products. The material is known for its resistance to weathering, corrosion, and chemicals, which makes it particularly popular in the construction industry.
PVC’s affordability and ease of processing make it an attractive option for manufacturers. Due to its lightweight, durable, and low-maintenance properties, it is often seen as an alternative to traditional building materials such as wood, metal, and concrete.
History of PVC
PVC was first discovered accidentally by German chemist Eugen Baumann in 1872. By the early 20th century, commercial uses for PVC began to emerge, especially during World War I when Germany started producing flexible and rigid PVC products as substitutes for corrosion-resistant metals.
Basic Forms of PVC
Plastic PVC comes in various forms, each offering specific properties for specific applications:
Flexible PVC: This PVC version is more flexible due to the addition of plasticisers. It’s ideal for wire and cable insulation and soft tubing applications.
Rigid (uPVC). Unplasticised, rigid PVC provides cost-effective protection from impact, weather and chemicals.
Chlorinated CPVC: CPVC with added chlorine offers superior resistance to chemicals, high temperatures and other substances, making it ideal for hot water pipes.
Molecularly Oriented PVC: This type improves its physical properties, such as stiffness, fatigue resistance, and elasticity, by reorganising its molecular structure.
Modified PVC: PVC-M is a modified PVC enhanced with toughening agents to improve toughness and impact resistance. It’s ideal for applications requiring extra durability.
Pros and Cons of Rigid & Flexible PVC
Both rigid and flexible PVC have distinct advantages and limitations that determine their use in various industries:
Property | Rigid PVC (uPVC) | Flexible PVC (PVC-P) |
Strengths | Low cost, high stiffness, good electrical insulation, chemical resistance, flame retardant, suitable for transparent applications | Flexible, high impact strength, good UV and chemical resistance, versatile, easy to process |
Low Cost | Yes | No |
High Stiffness | Yes | No |
Good Electrical Insulation | Yes | No |
Chemical Resistance | Yes | No |
Flame Retardant | Yes | No |
Transparency | Yes | No |
Limitations | Limitations | Limitations |
Brittleness at Low Temperatures | Yes | No |
Difficult to Melt | Yes | No |
Low Continuous Service Temperature | Yes | No |
Flexibility | No | Yes |
High Impact Strength | No | Yes |
Good UV and Chemical Resistance | No | Yes |
Versatile and Easy to Process | No | Yes |
Lower Chemical Resistance | No | Yes |
Plasticizer Migration | No | Yes |
Degradation at High Temperatures | No | Yes |
Typical Applications | Pipes and fittings, window frames, electrical conduit, signage | Wire and cable insulation, soft tubing, flooring, medical devices |
What is Chlorinated PVC (CPVC)?
CPVC is manufactured by chlorinating standard PVC resin, increasing its chlorine content from 56% to around 66%. This results in a material with enhanced durability, chemical stability, and flame retardancy. CPVC can also withstand higher temperatures, making it a preferred choice for hot water systems and chemical processing equipment.
How is PVC Manufactured?
PVC material is produced primarily through vinyl chloride monomer (VCM) polymerisation. Two popular manufacturing methods include:
- Suspension PVC (S-PVC) Process: This accounts for approximately 80% of global PVC production. The monomer is introduced into a pressure-tight reactor with a polymerisation initiator. Continuous mixing ensures uniform particle size, producing a PVC resin suitable for various plastic part.
- Bulk or Emulsion PVC (E-PVC) Process: In this method, vinyl chloride monomer is dispersed in water using surfactants. The resulting PVC is used in speciality applications such as coatings and spreadable pastes.
The main difference between S-PVC and E-PVC lies in their costs and flexibility. S-PVC is cheaper and more suited for rigid applications, while E-PVC is typically more expensive and used for flexible products like coatings and sprays.
Key Properties of PVC
PVC’s versatility stems from its wide array of beneficial properties:
- Electrical Insulation: PVC is an excellent dielectric wire and cable insulation material.
- Durability: PVC is a top choice for outdoor and long-lasting products because it is resistant to weathering, chemicals, and corrosion.
- Flame Retardancy: PVC is self-extinguishing due to its chlorine content, which gives it high fire resistance.
- Cost-Effective: PVC offers excellent physical properties at a low cost, with long life spans and minimal maintenance.
- Mechanical Strength: It is lightweight, rugged, and abrasion-resistant.
- Chemical Resistance: PVC is resistant to diluted acids, alkalis, and other chemicals, though specific grades may be attacked by more aggressive solvents like ketones.
Additives and Their Impact on PVC
Pure PVC is not thermally stable and can degrade during processing, which is why additives play a crucial role in its formulation:
- Plasticisers: Phthalates and adipates are used to make PVC flexible. They enhance PVC’s toughness, strength, and flexibility.
- Heat Stabilisers: These additives prevent PVC from degrading during processing by neutralising harmful by-products.
- Fillers: Added to improve stiffness, strength, and colour. Joint fillers include calcium carbonate, titanium dioxide, and talc.
- Lubricants: External lubricants improve processing, while internal lubricants reduce viscosity and prevent overheating.
Blending PVC with Thermoplastics
PVC is often blended with other thermoplastics to improve its properties for specific applications:
- PVC/Polyester Blends: Offers superior tensile strength and abrasion resistance.
- PVC/PU Blends: Increases chemical resistance and elasticity, particularly for biocompatible applications.
- PVC/NBR Blends: These are used in flexible, elastic materials that require good recovery characteristics.
Processing Conditions for PVC
PVC is processed using extrusion, injection moulding, and calendaring methods. Due to its sensitivity to heat, thermal stabilisation is necessary to avoid decomposition during processing. PVC also has a narrow processing temperature window, which requires careful control.
Recent advancements have even paved the way for 3D printing with PVC, opening new possibilities for additive manufacturing.
Is PVC Recyclable?
PVC is 100% recyclable and can be processed using mechanical, chemical, and feedstock recycling methods. Mechanical recycling involves shredding, grinding, and reprocessing PVC into new products. Chemical recycling breaks down the polymer into its monomers for reuse, while feedstock recycling recovers hydrogen chloride from PVC waste.
Global recycling initiatives are helping to create a circular economy for PVC. For example, Europe’s VinylPlus program and the U.S.’s +Vantage Vinyl initiative promote sustainability in the PVC industry.
Is PVC Toxic?
Due to chlorine and additives such as phthalates, PVC material has been under scrutiny. Some phthalates have raised health concerns, but ongoing research has determined that certain types are safe for use. Europe has also phased out lead-based stabilisers due to their harmful environmental impact.
Innovations in Bio-PVC
Recent innovations have focused on creating bio-based PVC from renewable sources such as non-food chain biomass. Companies like Ineos and Vynova are responsible for developing bio-PVC formulations, which help reduce the material’s environmental footprint.
Plastic PVC in Injection Moulding
Polyvinyl Chloride (PVC) is a versatile thermoplastic widely utilised in injection moulding, where heated PVC resin is injected into moulds to create complex shapes. Due to its adaptability, this method is widespread across construction, automotive, and medical industries.
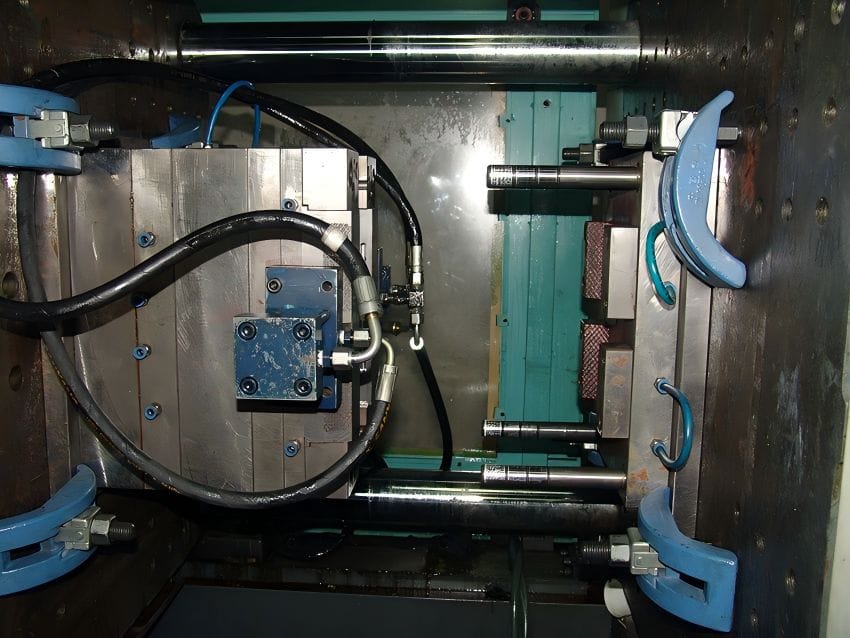
Plastic PVC resin can be enhanced with various additives to improve its flexibility and impact resistance, making it an ideal choice for multiple applications, including pipes, fittings, and medical devices. These modifications allow PVC to withstand stress and deformation, ensuring longevity and reliability in demanding environments.
Additionally, PVC exhibits excellent chemical resistance, enabling it to resist degradation from harsh chemicals and environmental factors. This durability further enhances its suitability for outdoor applications, such as construction materials and plumbing systems, where exposure to the elements is a concern. Flexibility, impact resistance, and chemical stability make modified PVC attractive across various industries, including healthcare, construction, and automotive sectors. Moreover, its low cost and ease of processing contribute to its widespread use and versatility in manufacturing.
However, PVC processing requires careful temperature regulation to prevent degradation, necessitating thermal stabilisers. Overall, its versatile properties and precise injection moulding make PVC an excellent material choice for high-quality components with long service life.
Conclusion
Polyvinyl Chloride (PVC) continues to be a versatile and widely used material in various industries. Its adaptability and cost-effectiveness make it a valuable resource in the construction and healthcare industries. With ongoing innovations in bio-PVC and recycling initiatives, PVC is evolving into a more sustainable option, ensuring its continued relevance in the years to come.